Purchasing
Sales Operations
Product Article Master
Logistics
Finance
- Accounts Payable
- Invoice verification & posting invoices
- Making payments to vendors & queries
- Goods receipt and invoice receipt clearance
- Analyze vendor open line items
- Overhead cost invoices
- MIRO Posting
- Accounts Recievables
- Scheduling a dunning run
- Settling customer payments & queries
- Self-billing of customer’s invoice
- Bank reconciliation
- Customer invoice clearance
- Sales Order Booking
- Daily Credit Run
- Releasing Green Orders
Market Research
Adjusting far-east orders in SAP
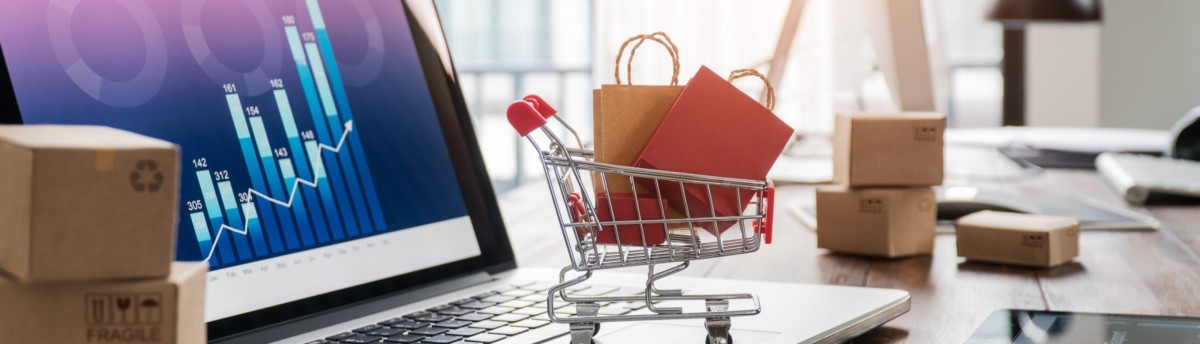
Würth Business Services offers a wide range of the Logistics Support services to ensure a seamless experience of shipment delivery for companies within the Würth Group. We aim to accelerate logistical operations by assisting Logistics teams in executing various processes. We have a team of experienced and well-trained professionals who excel in handling non-core processes.
Among many processes, Adjusting Far-East Orders in SAP is one of them. In this process, far-east purchasers update the required quantity of products in SAP system. We send this requirement to suppliers. Then we receive an invoice that mentions the available quantity from the suppliers. Our Logistics Team adjusts the quantities according to the requirement and availability. Furthermore, we create loading lists, commercial invoices, and packing lists for customs clearance. These invoices and lists are uploaded to the Transport Management Information System (TMIS) portal.
Work Flow
WORK FLOW OF THE PROCESS
01. Send
Send requirement from far-east purchasers to suppliers
02. Receive
Receive invoice for order from suppliers
03. Analyze
Analyze the available quantity mentioned in invoices
04. Adjust
Adjust the quantity as per requirement and availability
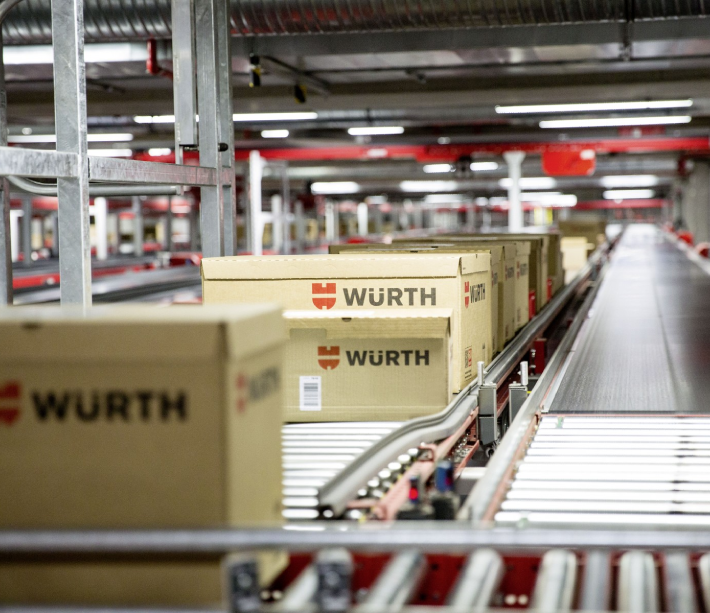
Benefits
Value-added
BENEFITS OF OUR CUSTOMERS
☞ Know the available quantity and adjust inventory levels
☞ Streamline the custom clearance process
☞ Authorize payments based on order details
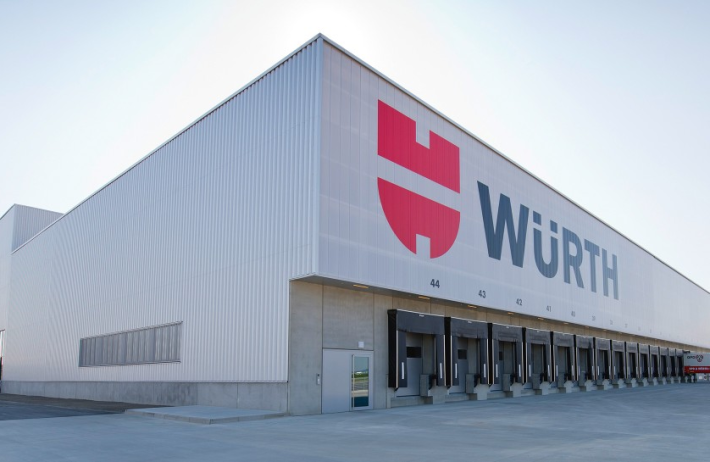
Transition
TIME TAKEN FOR TRANSITION
Step 1
Analysis of requirements – 1 Week
Step 2
Documentation – 1-2 Weeks
Step 3
Create framework – 1 Week
Step 4
Step-by-step implementation – 2 Weeks
Step 5
Transfer – 1 Week
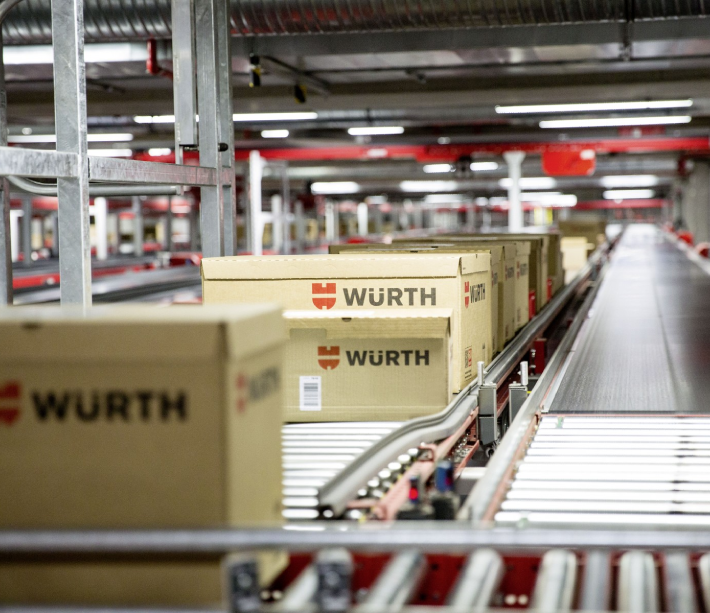
Case study:
Executing the Adjusting Far-East Orders Process for Streamlining Operations
Introduction:
Efficient management of far-east orders is crucial for smooth procurement and logistics operations. Würth Industrie Service GmbH & Co. KG identified the need to optimize the Adjusting Far-East Orders process to determine the available quantity of articles, adjust an inventory levels, and optimize customs clearance process. This case study highlights how we successfully handled the process, resulting in improved productivity and streamlined logistics management.
Problem:
Before transferring the process, Würth Industrie Service GmbH & Co. KG encountered different challenges in knowing the quantity of articles available after ordering. The lack of proper adjustment of the orders led to unpredictability in production schedules and adjustment of inventory levels. Managing the quantities, coordinating with suppliers, creating loading lists, commercial invoices, and packing lists required a lot of time and efforts, leading to delays, inaccuracies, and operational inefficiencies.
Solution:
To address these challenges, we implemented a comprehensive solution to streamline the Adjusting Far-East Order in SAP process. The key components of our solution included:
1. Supplier Communication: Our Logistics Support Team established communication channels with suppliers and sent the quantity requirements from the far-east purchasers. We coordinated with suppliers to determine the available quantity.
2. Updating quantity in SAP: Upon receiving invoices from suppliers, our team updated the quantity in SAP system. Through this system, our customers can determine the quantity that will be available for them. Accordingly, they can adjust inventory levels and prepare the customs clearance documents. This communication and updating the status in SAP leads to ease in collaboration.
3. Digital Document Management: We implemented a digital document management system such as a Transport Management Information System (TMIS) portal. We created loading lists, commercial invoices, and packing lists digitally. These documents were uploaded to the TMIS portal for customs clearance, eliminating the need for manual printing, scanning, and physical document management.
Results:
The implementation of the Adjusting Far-East Orders in SAP process yielded significant benefits for Würth Industrie Service GmbH & Co. KG. Key results included:
1. Improved Efficiency: The supplier communication, updating of status in SAP, and document management significantly improved operational efficiency. We handled the manual tasks and communication processes, enabling our customers to focus on higher-value activities and ensuring smoother logistics management.
2. Enhanced Accuracy: The seamless transfer of information from suppliers' invoices to our SAP system ensured accurate and up-to-date data, minimizing the risk of overstocking or stockouts.
3. Streamlined Customs Clearance: The digitization of loading lists, commercial invoices, and packing lists facilitated more efficient customs clearance process. Uploading these documents to the TMIS portal reduced administrative workload, improved traceability, and streamlined the overall customs clearance process.
Conclusion:
By streamlining the Adjusting Far-East Orders process, Würth Industrie Service GmbH & Co. KG. achieved significant improvements in efficiency, accuracy, and customs clearance process. The supplier communication, invoice processing, and digital document management reduced efforts, minimized errors, and enhanced overall productivity. We remain committed to leveraging technology and process optimization to streamline operations, enhance customer satisfaction, and drive overall business success.