Purchasing
Sales Operations
Product Article Master
Logistics
Finance
- Accounts Payable
- Invoice verification & posting invoices
- Making payments to vendors & queries
- Goods receipt and invoice receipt clearance
- Analyze vendor open line items
- Overhead cost invoices
- MIRO Posting
- Accounts Recievables
- Scheduling a dunning run
- Settling customer payments & queries
- Self-billing of customer’s invoice
- Bank reconciliation
- Customer Invoice Clearance
- Sales Order Booking
- Daily Credit Run
- Releasing Green Orders
Market Research
Delivery Date Change
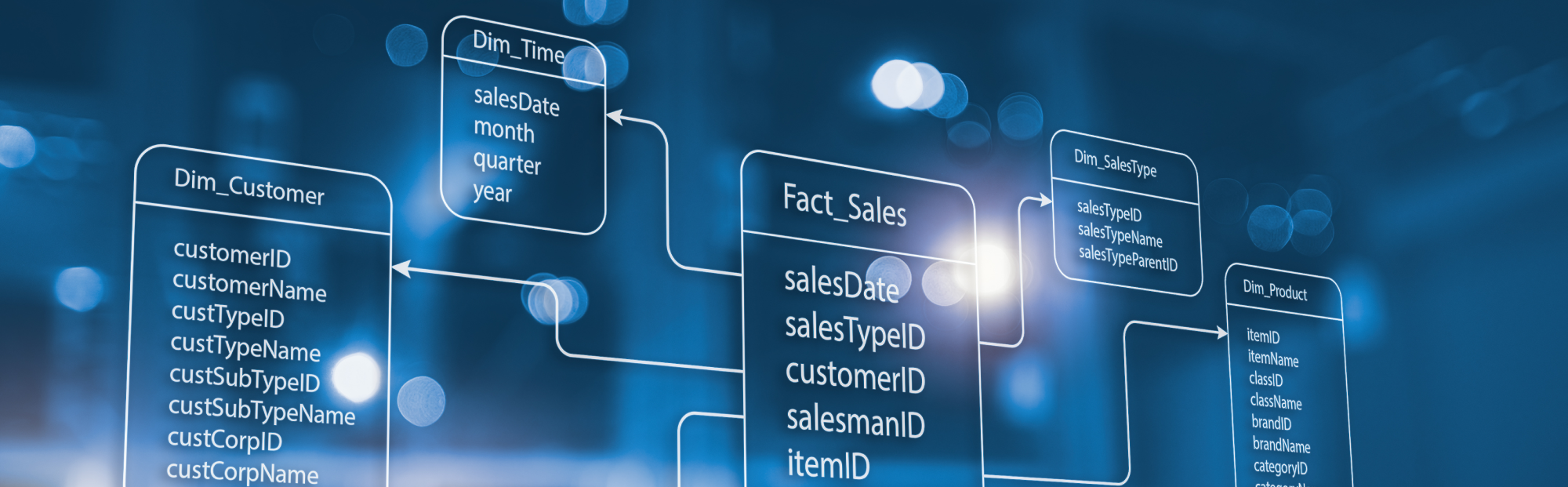
Würth Business Services handles the non-core Sales Operations to support your Sales Team in achieving the targets and registering a significant business growth. We handle many processes to help your business accelerate the Sales and Operations Planning (S&OP) tasks. Our services are aimed at driving profitability and providing rapid solutions.
Among many processes we handle, Delivery Date Change is one of the processes. In this process, we update the delivery date in the Enterprise Resource Planning (ERP) system as per the changes in customer requirements. Moreover, we update the quantity for rescheduling. This process provides an updated information about the delivery date. Furthermore, it enables planning the required quantity and stocking the articles to fulfil the demand.
Work Flow
WORK FLOW OF THE PROCESS
01. Receive
Receive a mail containing a file with changed delivery date
02. Select
Select that order from ERP system and change the delivery date
03. Send
Send confirmation about the change to the customer
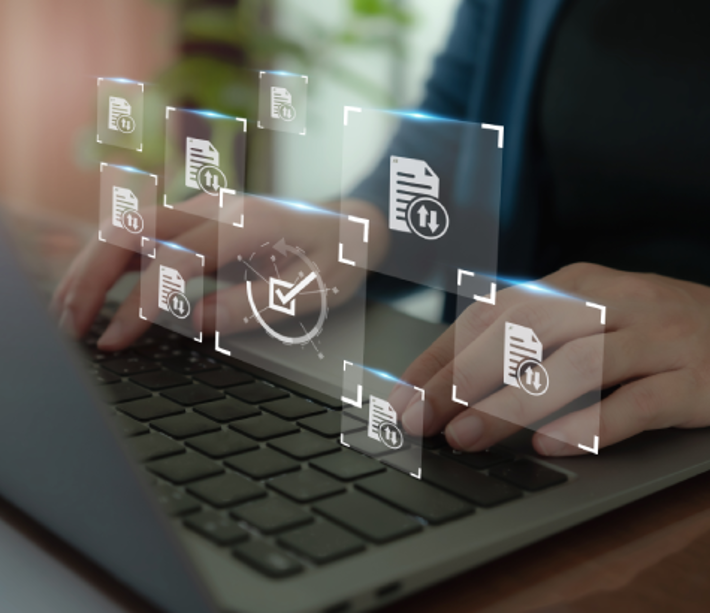
Benefits
Value-added
BENEFITS OF OUR CUSTOMERS
☞ Avail the updated information about the delivery dates
☞ Take follow-ups to avail order on time
☞ Plan orders and keep sufficient stocks at hand
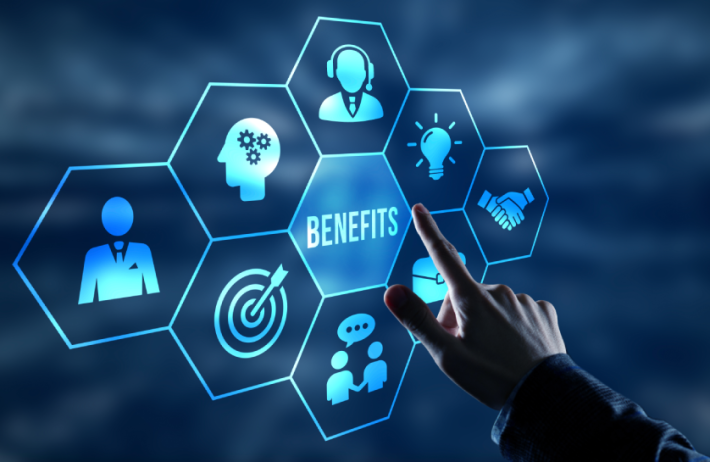
Transition
TIME TAKEN FOR TRANSITION
Step 1
Analysis of customer requirements – 1 Working Day
Step 2
Resource planning – 1 Working Day
Step 3
Tools requirement – 3 Working Days
Step 4
Training phase/Documentation – 2 Working Days
Step 5
Trial submission – 4 Working Days
Step 6
Transfer – 5 Working Days
For more assistance in understanding the transition process, kindly get in touch with us at contact-wbs@wuerth-industrie.com
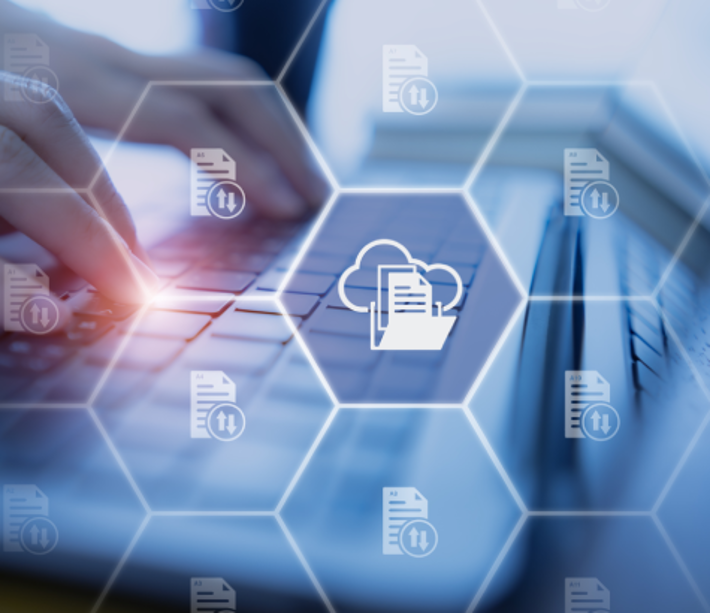
Case study:
Changing Delivery Dates for Giving Updated Information
Introduction:
Efficient delivery date management is crucial for meeting customer expectations and ensuring smooth order fulfillment. Our customer, Würth Industrie Service GmbH & Co. KG, recognized the need to update the changed delivery date in the Enterprise Resource Planning (ERP) system to store updated information. This case study delves into the Delivery Date Change process, in which we update the delivery dates based on changes in customer requirements. By manually adjusting delivery dates and quantities for rescheduling, we aim to provide accurate and updated information to facilitate efficient planning and inventory management.
Problem:
Our customer faced several challenges related to delivery date management. Lack of a structured process for updating delivery dates led to discrepancies between customer requirements and actual delivery schedules, resulting in confusion and dissatisfaction. Without real-time updates on delivery dates, our customer struggled to adjust production schedules and inventory levels accordingly. This, in turn, led to inefficiencies and delays in order fulfillment. Inconsistent delivery dates and delays in order delivery adversely impacted customer satisfaction and loyalty.
Solution:
Recognizing the need to address the challenges in delivery date management, we implemented a manual Delivery Date Change process. Our key solutions included:
1. Customer Communication: We proactively communicated with customers to understand changes in delivery requirements, such as revised deadlines or quantity adjustments.
2. ERP System Updates: Using the information provided by customers, we manually updated delivery dates and quantities in the ERP system based on the files sent by the customer. This way, the ERP system reflected the revised order specifications accurately.
Results:
The implementation of the Delivery Date Change process yielded improvements in delivery date management and customer satisfaction for Würth Industrie Service GmbH & Co. KG. The key results included:
1. Improved Accuracy: By manually updating delivery dates in the ERP system, we ensured that customer requirements were accurately addressed, reducing the likelihood of miscommunication and errors.
2. Enhanced Planning: Real-time updates on delivery dates enabled the company to adjust production schedules and inventory levels promptly, leading to more efficient resource allocation and order fulfilment than before.
3. Enhanced Customer Satisfaction: With accurate and updated delivery information, we achieved a reduction in delivery-related complaints and a noticeable increase in customer satisfaction scores.
4. Time Saving: Our approach led to significant time savings per month. We saved nearly 50 hours for our customer in a month. This saved time can be utilized for executing different core operations.
Conclusion:
By transferring the Delivery Date Change process, we addressed challenges related to delivery date management and enhanced customer satisfaction. With meticulous manual updates and proactive communication with customers, we helped in streamlining order fulfillment processes and meeting customer expectations effectively.