Purchasing
Sales Operations
Product Article Master
Logistics
Finance
- Accounts Payable
- Invoice verification & posting invoices
- Making payments to vendors & queries
- Goods receipt and invoice receipt clearance
- Analyze vendor open line items
- Overhead cost invoices
- MIRO Posting
- Accounts Recievables
- Scheduling a dunning run
- Settling customer payments & queries
- Self-billing of customer’s invoice
- Bank reconciliation
- Customer Invoice Clearance
- Sales Order Booking
- Daily Credit Run
- Releasing Green Orders
Market Research
Pack Size Change

Würth Business Services handles the article data management operations related to the Product Article Master Department. We handle a wide range of processes for maintaining the accurate and standardized article data through SAP system. Our Team utilizes the advanced tools and software, implements standard procedures, maintains quality standards, and efficiently manages and maintains the article data.
Among many processes, Pack Size Change is one of the processes handled by us. In this process, if the customer wishes to change the pack size, we change in pack size the Enterprise Resource Planning (ERP) system. The size of certain packaging units are already entered in the system as the requirements of customer. However, owing to circumstances, if the customer wishes a special pack size, we change the pack size in the ERP system, so supplier will possess the knowledge of the change and send accordingly.
Work Flow
WORK FLOW OF THE PROCESS
01. Receive
Receive old and new pack size details and verify quality checklist and the status for the old pack size
02. Create
Create a new pack size and pack quantity and add details such as buyer code & price
03. Mention
Mention the quality checklist same as the old pack size and change the status of the pack size to active upon creating new pack size
04. Details
If instructed in the details received, discontinue the old pack size with the follow-up material number (newly created material number)
05. Notify
Notify the customer that a new pack size has been created
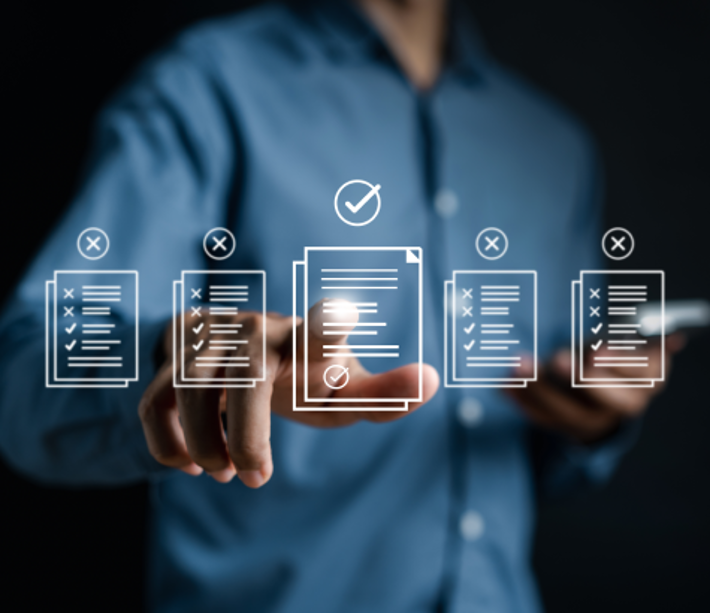
Benefits
Value-added
BENEFITS OF OUR CUSTOMERS
☞ Save time in manually creating new pack sizes
☞ Provide the accurate knowledge of pack sizes to suppliers
☞ Experienced and trained professionals to ensure accuracy in process execution
☞ Focus on core operations
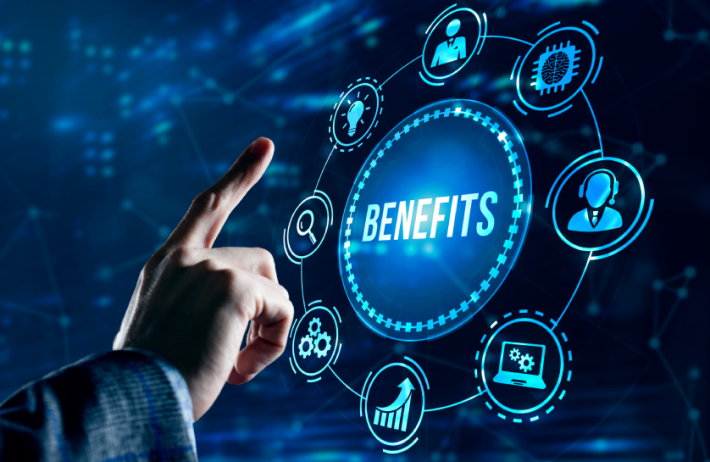
Transition
TIME TAKEN FOR TRANSITION
Step 1
Analysis of customer requirements – 1 Day
Step 2
Resource planning – 1 Day
Step 3
Tools requirement – 3 Days
Step 4
Training phase/Documentation – 2 Days
Step 5
Trial submission – 5 Days
Step 6
Transfer – 1 Week
For more assistance in understanding the transition process, kindly get in touch with us at contact-wbs@wuerth-industrie.com
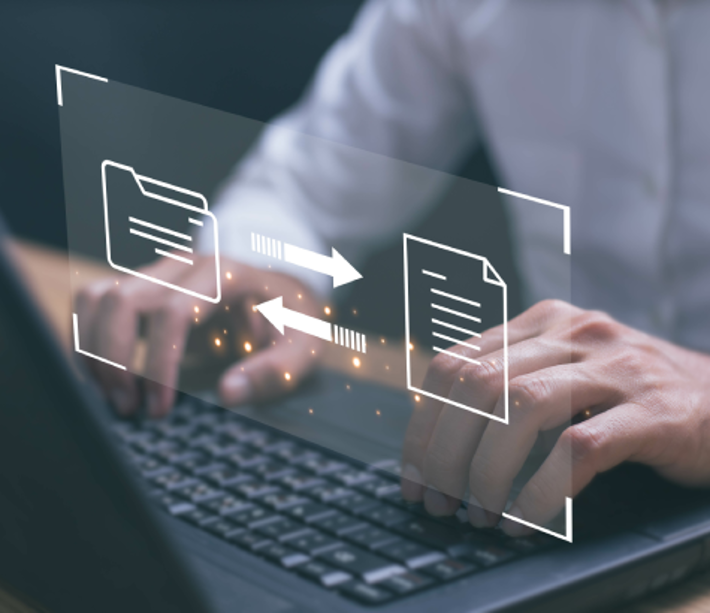
Case study:
Optimizing Pack Size Change Process for Enhanced Product Offerings
Introduction:
Maintaining an updated and flexible product catalog is crucial for meeting market demands and customer preferences. Our customer, Würth Industrie Service GmbH & Co. KG, recognized the need to maintaining the pack size details. This case study explores the manual Pack Size Change process, in which a dedicated team receives details about old and new pack size specifications, verifies quality checklists and the status for the old pack size, and creates a new pack size. Then our team adds details such as buyer code and price, ensures consistent quality checklists, changes the status of the pack size to active and notifies customers of the change. This meticulous process aims to enhance product offerings without the involvement of automation.
Problem:
Our customer faced challenges in efficiently managing pack size changes manually. The customer needed to invest a considerable number of man-hours to execute the process. Furthermore, it led to potential errors in data entry, delays in creating new pack sizes and difficulties in maintaining consistency across product details. These inefficiencies hindered the company's ability to swiftly adapt to market demands, resulting in delays in product updates and potential customer dissatisfaction. This impacted overall product catalog management efficiency.
Solution:
Recognizing the need to enhance their Pack Size Change process, we adopted a systematic approach to improve accuracy and order processing efficiency. Our key solutions included:
1. Detailed Information Reception: We initiated a manual process to receive detailed information about old and new pack size specifications, ensuring a comprehensive understanding of the required changes.
2. Quality Checklist Verification: Despite manual processing, our dedicated team verified quality checklists and the status for the old pack size to maintain product consistency.
3. Accurate Data Entry: We actively ensured accurate data entry when creating a new pack size, adding details such as buyer code and price with precision.
4. Consistent Quality Checklists: Meticulously maintaining quality checklists consistent with the old pack size, we ensured uniformity in product offerings.
5. Timely Customer Notification: Our team actively notified customers of the new pack size, ensuring transparency and providing customers with updated product information.
Results:
The changes implemented in the Pack Size Change process led to significant improvements in product catalog management efficiency and accuracy for Würth Industrie Service GmbH & Co. KG. The key results included:
1. Efficient Pack Size Changes: By implementing accurate data entry and quality checklist verification, we reduced the time taken to implement pack size changes significantly, ensuring timely updates to product offerings.
2. Data Accuracy Improvement: Despite manual processes, data accuracy improved considerably, reducing errors in product details and enhancing overall product catalog consistency.
3. Enhanced Customer Satisfaction: Timely customer notifications resulted in an increase in customer satisfaction, demonstrating the commitment to keeping customers informed about product changes.
4. Time Saving: Our approach led to significant time savings per month. We saved nearly 48 hours for our customer in a month. This saved time can be utilized for executing different core operations.
Conclusion:
By transferring the Pack Size Change process, our customer ensured an updated and flexible product catalog. By implementing accurate data entry, quality checklist verification and proactive customer notifications, we successfully improved product catalog management efficiency and customer satisfaction. The results underscore the value of manual processes in adapting to market demands and delivering accurate product information.