Purchasing
Sales Operations
Product Article Master
Logistics
Finance
- Accounts Payable
- Invoice verification & posting invoices
- Making payments to vendors & queries
- Goods receipt and invoice receipt clearance
- Analyze vendor open line items
- Overhead cost invoices
- MIRO Posting
- Accounts Recievables
- Scheduling a dunning run
- Settling customer payments & queries
- Self-billing of customer’s invoice
- Bank reconciliation
- Customer invoice clearance
- Sales Order Booking
- Daily Credit Run
- Releasing Green Orders
Market Research
Creation of shipments
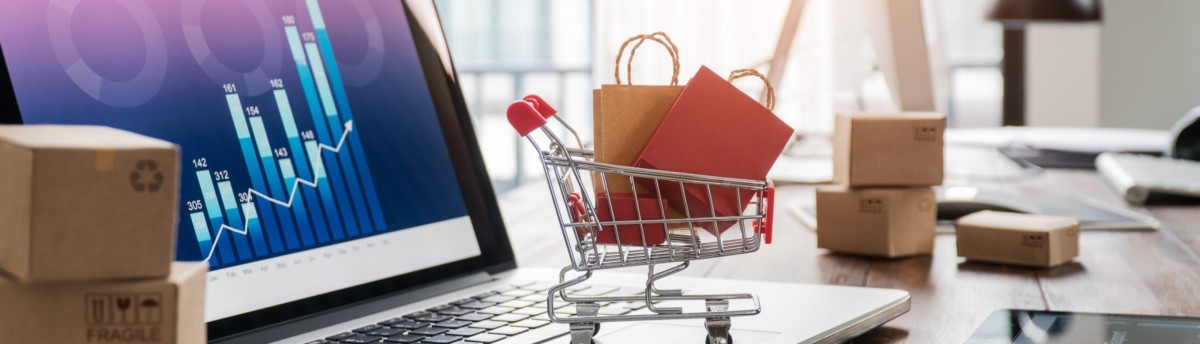
Würth Business Services offers a wide range of the Logistics Support services to ensure a seamless experience of shipment delivery for companies within the Würth Group. We aim to accelerate logistical operations by assisting Logistics teams in executing various processes. We have a team of experienced and well-trained professionals who excel in handling non-core processes.
Among many processes, Creation of Shipments is one of them. In this process, we organize road shipment(s) within the European Union (EU) countries that have the Ex Works (EXW) incoterm. The shipments are organized on the Transport Management Information System (TMIS) portal. These shipments also include the direct deliveries that need to be picked up from the supplier and delivered to the customer. We also organize return shipments from the customer to the warehouse. The data related to all the organized shipments is maintained in the system for the future reference.
Work Flow
WORK FLOW OF THE PROCESS
01. Organize
Organize the shipments with the help of shipment details received
02. Register
Register all the shipment details, such as order and material number, quantity and number of packages, Würth article number, and contact details of the consigner
03. Create
Create the shipment number and label for future reference and tracking
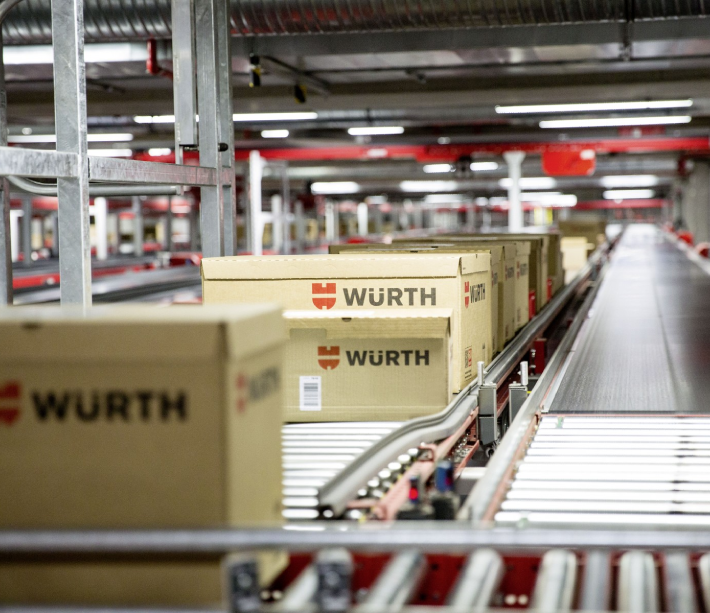
Benefits
Value-added
BENEFITS OF OUR CUSTOMERS
☞ Transport goods from the point of departure to the point of consumption without any hassles
☞ Smooth procurement process and maintenance of the correct Würth article data
☞ Simplified process for identifying goods in a warehouse and prioritization if necessary
☞ Smooth transfer of goods and clear communication
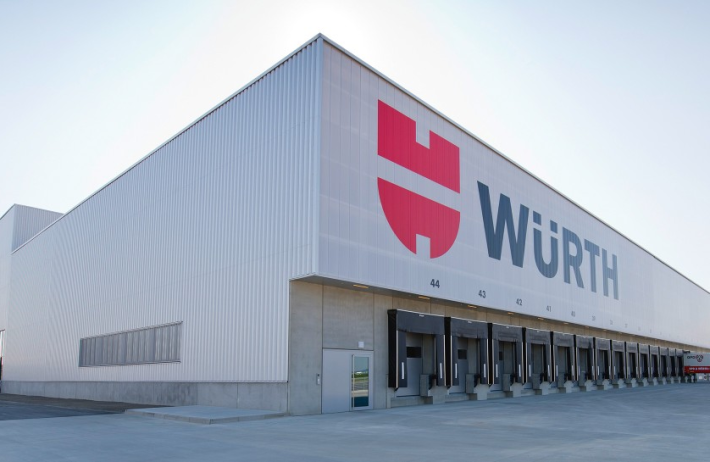
Transition
TIME TAKEN FOR TRANSITION
Step 1
Analysis of requirements – 1-2 Week
Step 2
Documentation – 1 Week
Step 3
Transfer – 1 Week
Step 4
Step-by-step implementation – 1 Week
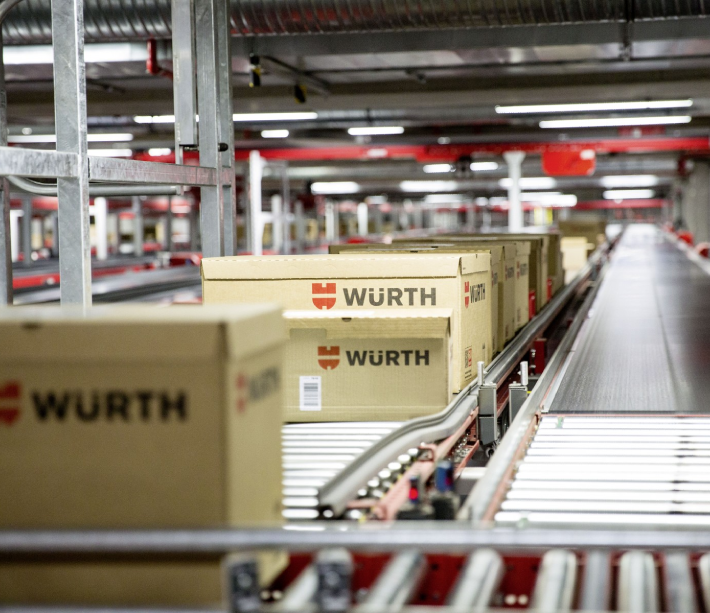
Case study:
Streamlining the Creation of Shipments Process
Introduction:
The Creation of Shipments process is a critical aspect of supply chain management, particularly when dealing with road shipments within the European Union (EU) countries using the Ex Works (EXW) incoterm. Our customer, Würth Industrie Service GmbH & Co. KG, recognized the need for organizing the shipments and data related to those shipments. We organized shipments using a manual process and transformed the process to enhance efficiency and accuracy.
Problem:
Our customer faced several challenges within their existing Creation of Shipments process. The complexity of EXW Incoterm was one of the major issues. The EXW incoterm requires the buyer to arrange the pickup of goods directly from the supplier's location. Coordinating these pickups and ensuring timely delivery to the customer's destination proved to be intricate and time-consuming. Moreover, Due to the absence of a centralized system, tracking and monitoring shipments in real-time became a challenge. This led to delays in identifying potential issues and proactively addressing them. The process of organizing return shipments from customers back to the warehouse was intricate. There were delays and errors in coordinating the return logistics.
Solution:
To overcome these challenges and streamline the Creation of Shipments process, we implemented a comprehensive solution that integrated technology and accuracy through manual process. We introduced a centralized Transport Management Information System (TMIS) portal that acted as a hub for all shipment-related activities. This portal allowed us to input shipment details, track shipments in real-time, and communicate with suppliers, customers, and logistics partners.
All the information related to shipments, including pickup requests, delivery instructions, and return shipments, was stored centrally in the TMIS portal. Furthermore, there was a manual data entry and our professionals diligently entered information with the highest accuracy. We also established a standardized operating procedure for EXW incoterm shipments, ensuring that pickups, deliveries, and returns followed a consistent and efficient process.
Results:
The implementation of the new solution brought about significant improvements for Würth Industrie Service GmbH & Co. KG. The key results included:
1. Enhanced Visibility: Real-time tracking through the TMIS portal provided increased visibility into shipment statuses, enabling proactive issue resolution and better customer communication.
2. Reduced Errors: With standardized processes and centralized data, errors related to shipment details and communication were greatly reduced.
3. Cost Savings: The streamlined process and reduced errors led to cost savings associated with fewer delays, improved resource allocation, and better utilization of logistics resources.
4. Time Savings: Our approach led to significant time savings per month. We saved nearly 147 hours for our customer in a month. This saved time can be utilized for executing different core operations.
Conclusion:
The transformation of the Creation of Shipments process to a standardized system brought about remarkable improvements. By implementing a TMIS portal and leveraging systematic process, we addressed the challenges posed by EXW incoterm shipments. The results included enhanced efficiency, reduced errors, increased visibility, and ultimately, improved customer satisfaction. This case study underscores the transformative power of technology and process optimization in supply chain management.