Purchasing
Sales Operations
Product Article Master
Logistics
Finance
- Accounts Payable
- Invoice verification & posting invoices
- Making payments to vendors & queries
- Goods receipt and invoice receipt clearance
- Analyze vendor open line items
- Overhead cost invoices
- MIRO Posting
- Accounts Recievables
- Scheduling a dunning run
- Settling customer payments & queries
- Self-billing of customer’s invoice
- Bank reconciliation
- Customer Invoice Clearance
- Sales Order Booking
- Daily Credit Run
- Releasing Green Orders
Market Research
Stock Update Overview
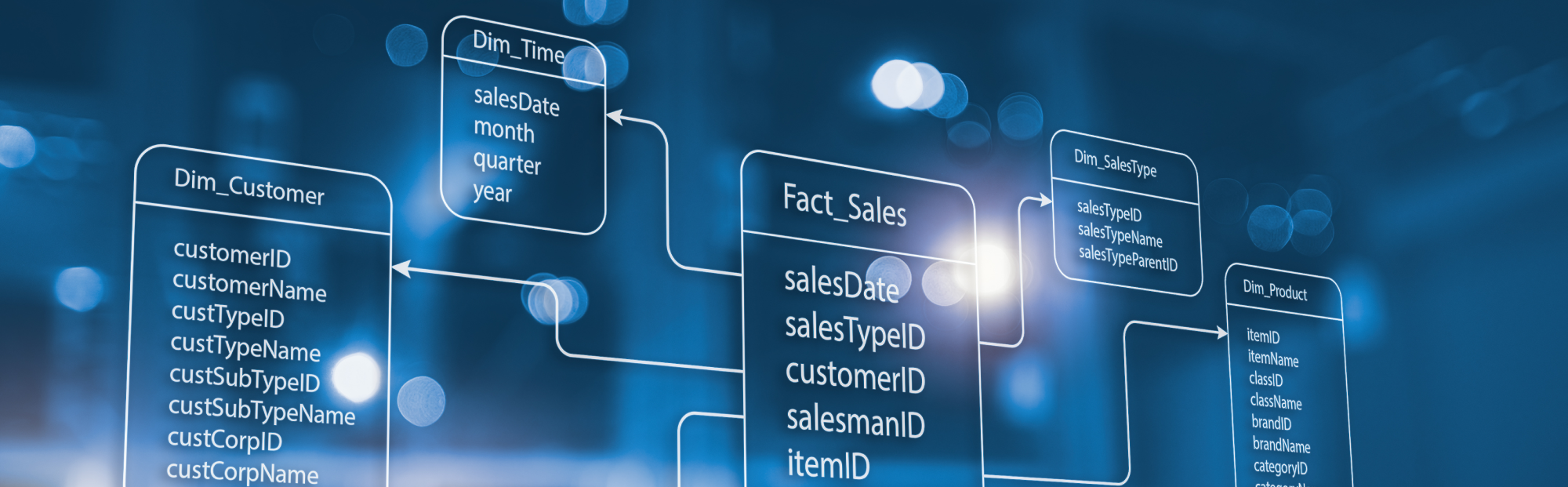
Würth Business Services handles the non-core Sales Operations to support your Sales Team in achieving the targets and registering a significant business growth. We handle many processes to help your business accelerate the Sales and Operations Planning (S&OP) tasks. Our services are aimed at driving profitability and providing rapid solutions.
Among many processes we handle, Stock Update Overview is one of the processes. In this process, we provide an overview of stocks related to open orders, demand from customers and possible delivery dates. This overview is essential to determine the stock availability, avoid overstocking or understocking and fulfil the demand of customers successfully.
Work Flow
WORK FLOW OF THE PROCESS
01. Check Available
Check open order quantity, delivery date and available stock
02. Check Demand
Check the demand at customer locations
03. Delivery Date
Check planned delivery date
04. Send
Send the updated list to customers
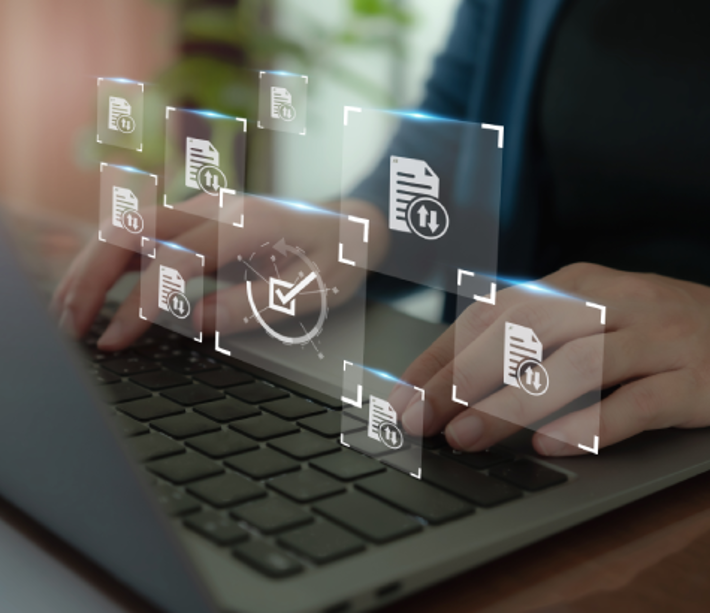
Benefits
Value-added
BENEFITS OF OUR CUSTOMERS
☞ Avail updated information on stock availability
☞ Plan deliveries accordingly
☞ Achieve customer satisfaction with proper planning
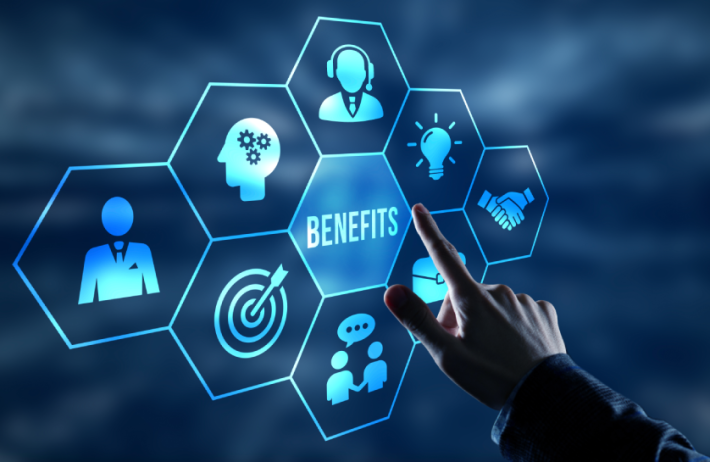
Transition
TIME TAKEN FOR TRANSITION
Step 1
Analysis of customer requirements – 1 Working Day
Step 2
Resource planning – 1 Working Day
Step 3
Tools requirement – 3 Working Days
Step 4
Training phase/Documentation – 2 Working Days
Step 5
Trial submission – 5 Working Days
Step 6
Transfer – 5 Working Days
For more assistance in understanding the transition process, kindly get in touch with us at contact-wbs@wuerth-industrie.com
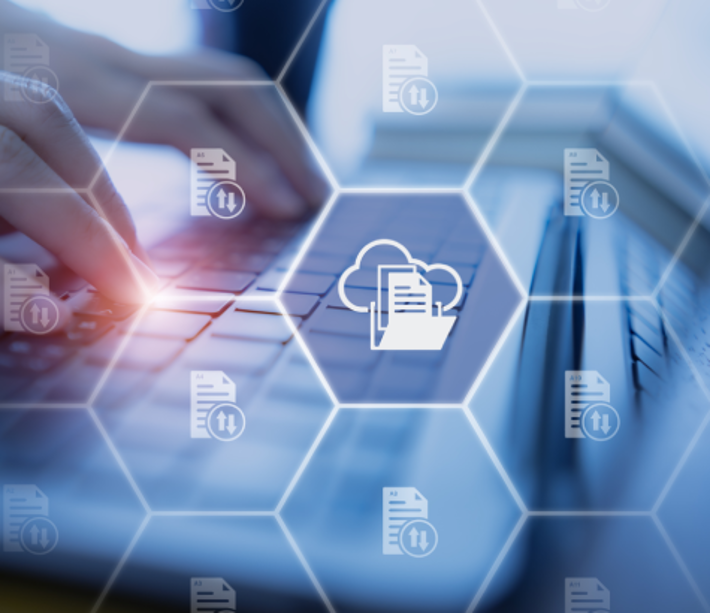
Case study:
Optimizing Inventory Management through Stock Update Overview
Introduction:
Effective inventory management is essential for businesses to meet customer demand, maintain stocks and maximize profitability. Our customer, Würth Industrie Service GmbH & Co. KG, recognized the need to gain updates on stocks. This case study explores the Stock Update Overview process, in which we provide a comprehensive view of stock levels related to open orders, customer demand and delivery dates. By manually compiling and analyzing this data, we aim to optimize inventory levels, mitigate stock-related challenges and enhance customer satisfaction.
Problem:
Our customer encountered various challenges in inventory management. Without a centralized overview of stock levels and demand, the customer struggled to assess inventory needs accurately. The absence of real-time data on stock availability hindered the ability to make informed decisions regarding order fulfillment. The customer needed to invest a considerable number of man-hours to update stocks.
Solution:
Recognizing the need to tackle challenges in inventory management, we adopted a manual Stock Update Overview process. Our key solutions included:
1. Data Collection and Analysis: We manually collected data on stock levels, open orders and customer demand from various sources.
2. Compilation of Stock Overview: Using the collected data, we compiled a comprehensive overview of stock availability, open orders and expected delivery dates. This overview provided insights into current inventory levels and anticipated demand.
3. Inventory Planning and Optimization: Armed with the stock update overview, our customer could plan inventory management more effectively than before. This ensured optimal stock levels to meet customer demands while minimizing excess inventory.
Results:
The implementation of the Stock Update Overview process yielded significant improvements in inventory management for Würth Industrie Service GmbH & Co. KG. The key results included:
1. Enhanced Visibility: The manual compilation of stock data provided the customer with real-time visibility into inventory levels, enabling proactive decision-making and order fulfillment.
2. Improved Customer Satisfaction: With better inventory planning and optimized stock levels, the customer achieved reduction in stockouts and order delays.
3. Cost Savings: By avoiding overstocking and reducing stockouts, the customer achieved cost savings associated with inventory carrying costs and expedited shipping expenses.
4. Time Saving: Our approach led to time savings per month. We saved nearly 13 hours for our customer in a month. This saved time can be utilized for executing different core operations.
Conclusion:
By transferring the Stock Update Overview process, our customer optimized inventory management and reduced operational costs. By implementing efficient approach, we carried out data collection and analysis to help the customer make informed decisions and achieve greater efficiency in inventory planning. Moving forward, the customer continues to refine and streamline the process to maintain optimal inventory levels and meet evolving customer demands.