Purchasing
Sales Operations
Product Article Master
Logistics
Finance
- Accounts Payable
- Invoice verification & posting invoices
- Making payments to vendors & queries
- Goods receipt and invoice receipt clearance
- Analyze vendor open line items
- Overhead cost invoices
- MIRO Posting
- Accounts Recievables
- Scheduling a dunning run
- Settling customer payments & queries
- Self-billing of customer’s invoice
- Bank reconciliation
- Sales Order Booking
- Daily Credit Run
- Releasing Green Orders
Market Research
Tracking of shipment and ETA adjustment
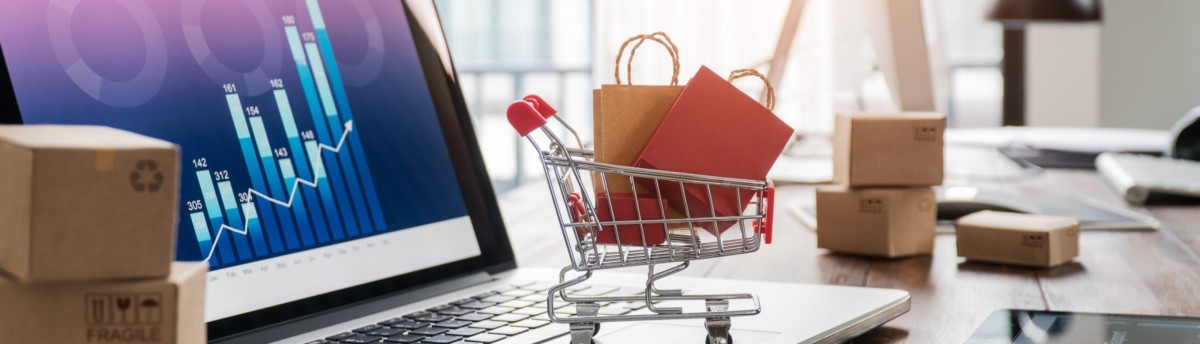
Würth Business Services offers a wide range of the Logistics Support services to ensure a seamless experience of shipment delivery for companies within the Würth Group. We aim to accelerate logistical operations by assisting Logistics teams in executing various processes. We have a team of experienced and well-trained professionals who excel in handling non-core processes.
Among many processes, Tracking of Shipment and ETA Adjustment is one of them. This process involves the Tracking of Shipment using the container number and the vessel number. We avail the information about the Estimated Time of Arrival (ETA) of the vessel at the port using these details. Furthermore, we update this ETA in the Transport Management Information System (TMIS). However, under the ETA Adjustment process, we update the changes in ETA in TMIS.
Work Flow
WORK FLOW OF THE PROCESS
01. Track
Track the shipment using container number and vessel number received from the customer
02. Update
Update the ETA information in TMIS
03. Adjust
Adjust the ETA based on the changes in schedule
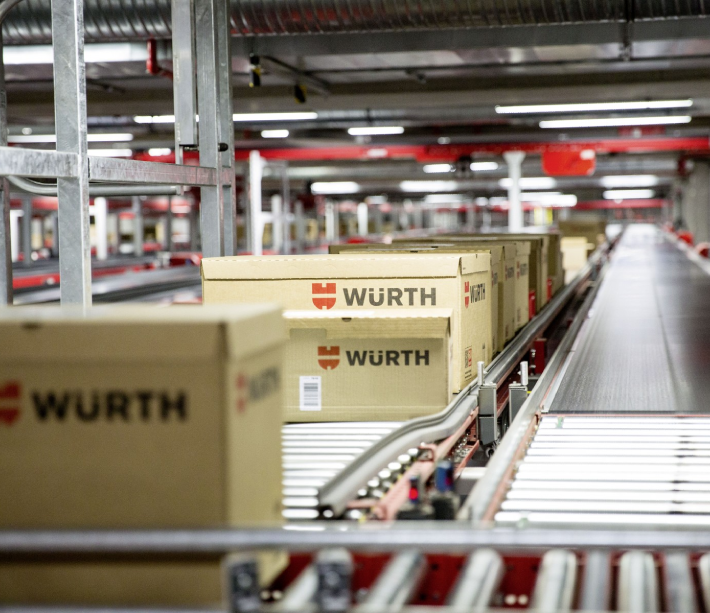
Benefits
Value-added
BENEFITS OF OUR CUSTOMERS
☞ Predict the delivery time by tracking shipments
☞ Manage the warehouse space for newly-arriving shipments
☞ Prepare documents for customs clearance
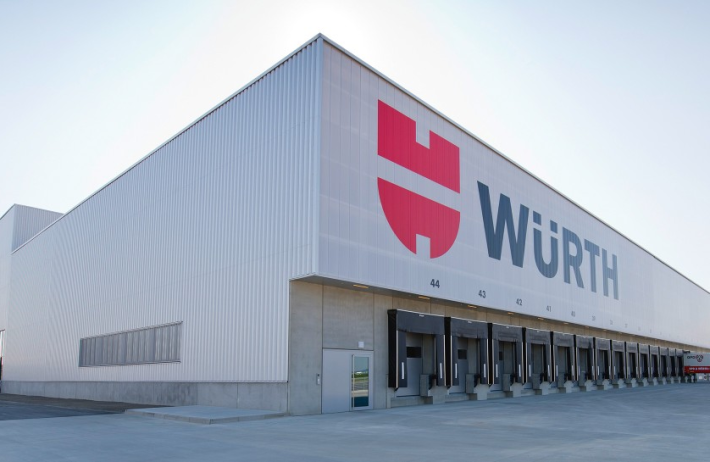
Transition
TIME TAKEN FOR TRANSITION
Step 1
Analysis of requirements – 2 Weeks
Step 2
Documentation – 2 Weeks
Step 3
Transfer – 2 Weeks
Step 4
Step-by-step implementation – 2 Weeks
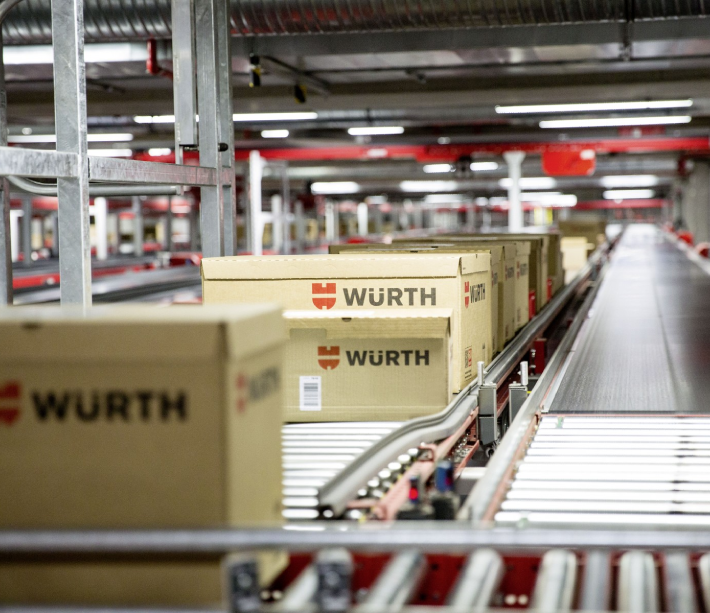
Case study:
Enhancing Shipment Tracking and ETA Adjustment for Accurate Delivery Planning
Introduction:
In the dynamic world of logistics and shipping, accurate tracking of shipments and timely adjustments to Estimated Time of Arrival (ETA) play a pivotal role in efficient supply chain management. Our customer, Wuerth Logistics Deutschland GmbH, determined the need for accurate tracking and knowing the ETA. We use container and vessel numbers to monitor shipment progress and update the ETA information in the Transport Management Information System (TMIS). By meticulously tracking shipments and adjusting ETA details, we aim to optimize delivery planning and ensure timely order fulfilment.
Problem:
Our customer encountered challenges in accurately tracking shipments and keeping ETA information up to date. Furthermore, a lot of time needed to invest in tracking and adjusting the ETA, which, in turn, led to potential delays, inaccuracies in ETA updates, and difficulties in coordinating with various stakeholders. This inefficiency restrained the company's ability to maintain reliable delivery schedules and manage customer expectations.
Solution:
Recognizing the need to streamline the Shipment Tracking and ETA Adjustment process, we adopted the systematic approach to improve the shipment visibility and ETA accuracy. We initiated a manual process to track shipments using container and vessel numbers. This step ensured the monitoring of the real-time shipment progress accurately. Moreover, based on the tracked shipment progress, we manually gathered information about the Estimated Time of Arrival (ETA) of the vessel at the port. This information was crucial for effective delivery planning. Under the ETA Adjustment process, we manually updated changes in ETA in the TMIS system. This step ensured that accurate ETA information was available for all stakeholders involved in the supply chain.
Results:
The changes implemented in the manual Shipment Tracking and ETA Adjustment process led to significant improvements in delivery planning accuracy and customer satisfaction for Wuerth Logistics Deutschland GmbH. Our key results included:
1. Timely Delivery Planning: By employing meticulous shipment tracking and ETA adjustment, we achieved an increase in accurate delivery planning. This minimized the risk of delivery delays and enhanced customer satisfaction.
2. Accurate ETA Information: The manual ETA adjustment process reduced inaccuracies in ETA updates. Accurate ETA information enabled better coordination among stakeholders and improved overall supply chain efficiency.
3. Strengthened Stakeholder Collaboration: With accurate and reliable ETA information, we experienced an increase in collaboration and trust among stakeholders. Accurate updates contributed to better communication and aligned expectations.
4. Time Savings: Our approach led to significant time savings per month. We saved nearly 105 hours for our customer in a month. This saved time can be utilized for executing different core operations.
Conclusion:
Our customer, Wuerth Logistics Deutschland GmbH, acquired accurate Shipment Tracking and ETA Adjustment process in ensuring accurate delivery planning and stakeholder collaboration. By implementing a comprehensive shipment tracking and ETA adjustment process, we successfully improved delivery planning accuracy, stakeholder communication, and overall supply chain efficiency. While automation was not involved, the results highlight the value of a well-executed Shipment Tracking and ETA Adjustment process in maintaining effective logistics practices and delivering timely customer solutions.