Purchasing
Sales Operations
Product Article Master
Logistics
Finance
- Accounts Payable
- Invoice verification & posting invoices
- Making payments to vendors & queries
- Goods receipt and invoice receipt clearance
- Analyze vendor open line items
- Overhead cost invoices
- MIRO Posting
- Accounts Recievables
- Scheduling a dunning run
- Settling customer payments & queries
- Self-billing of customer’s invoice
- Bank reconciliation
- Customer Invoice Clearance
- Sales Order Booking
- Daily Credit Run
- Releasing Green Orders
Market Research
INSPECTION PLAN CREATION
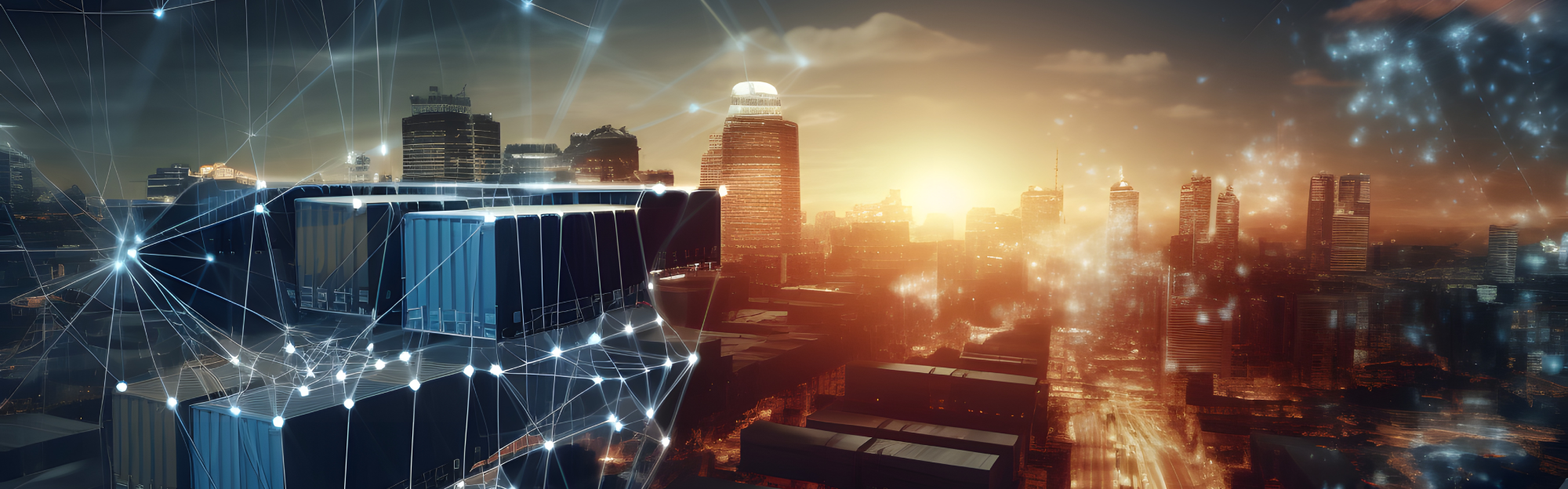
The Purchasing Department of Würth Business Services is equipped with a team of highly experienced procurement and purchasing professionals. We are instrumental in fulfilling the business-specific requirements by handling different processes related to Purchasing and serving customers across the globe. Among many non-core procurement and Purchasing-related processes handled by us, Inspection Plan Creation is one of the major processes.
In this process, our team creates a checklist for physical inspection of an article. This checklist ensures that quality standards are met and the customer requirements are fulfilled. We collaborate with our customers to obtain all the documents and information needed for creating a checklist. Based on an extensive analysis, we determine the parameters to be checked, create a thorough plan, and submit it in the Enterprise Resource Planning (ERP) system. So whenever you source the articles from the suppliers, you already possess an inspection plan to check them.
Work Flow
WORK FLOW OF THE PROCESS
01. Obtain
Obtain drawings & specifications for articles
02. Analyze
Analyze articles and compare them with standard parts
03. Devise
Devise major attributes and parameters to be checked
04. Create
Create a thorough inspection plan and checklists
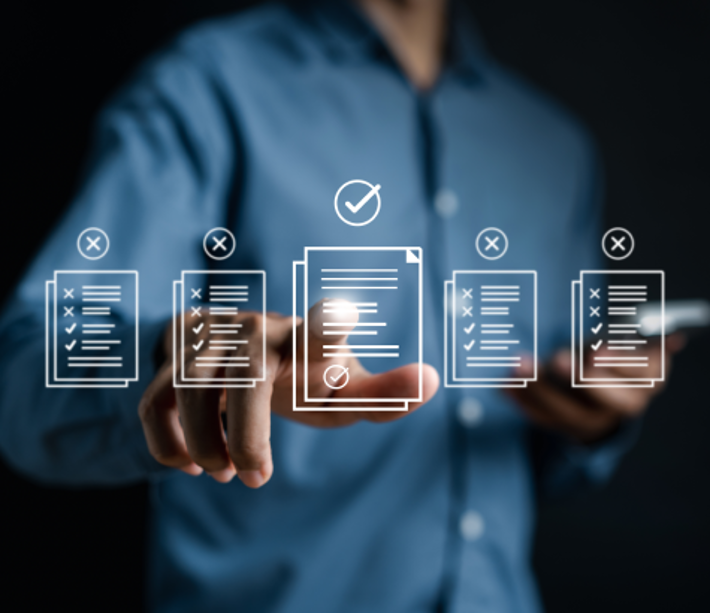
Benefits
Value-added
BENEFITS OF OUR CUSTOMERS
☞ Get precise, customized and reliable inspection plans
☞ Streamline and speed up physical inspection process
☞ Save time and costs incurred in reproduction of articles
☞ Throughout support and feedback incorporation
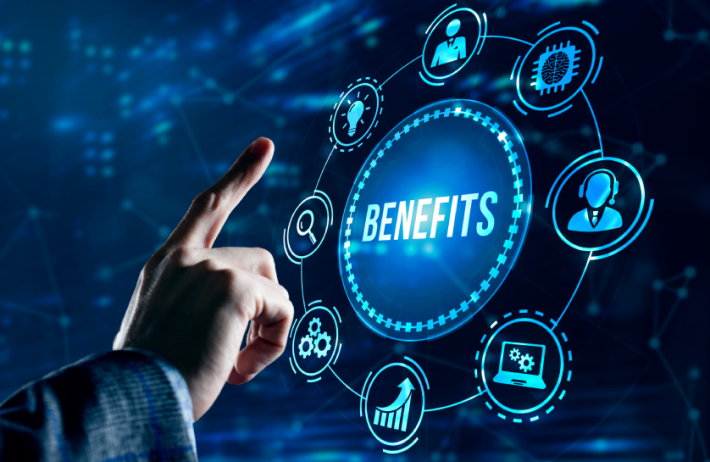
Transition
TIME TAKEN FOR TRANSITION
Step 1
Analysis of requirements – 1 Week
Step 2
Documentation – 1-2 Weeks
Step 3
Create framework – 1 Week
Step 4
Step-by-step implementation – 2 Weeks
Step 5
Transfer – 1 Week
For more assistance in understanding the transition process, kindly get in touch with us at contact-wbs@wuerth-industrie.com
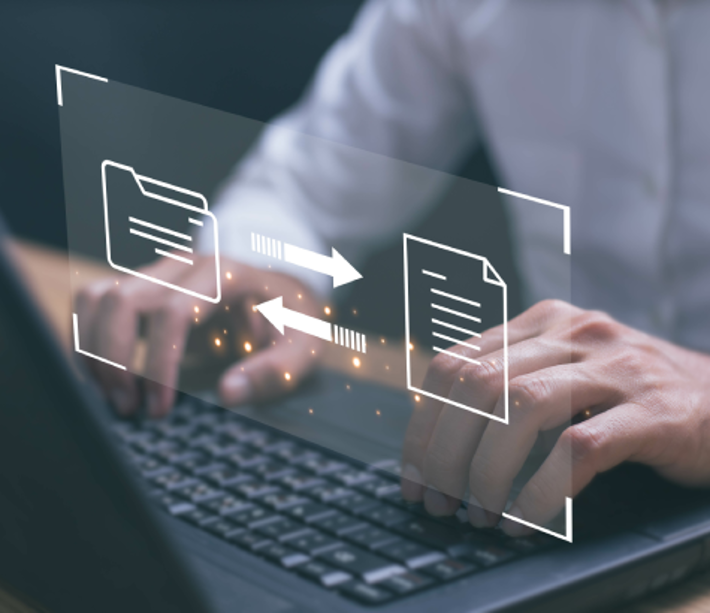
Case study:
Optimizing Inspection Plan Creation for Precision and Quality Assurance
Introduction:
Ensuring the quality and precision of manufactured articles is paramount for meeting industry standards and customer expectations. Our customer, Würth Industrie Service GmbH & Co. KG, recognized the need to create plans for inspections and speed up physical inspection activity. This case study explores the manual Inspection Plan Creation process, in which our dedicated team obtains drawings and specifications for articles, analyzes articles comparing them with standard parts and devises major attributes and parameters to be checked. Then we create a comprehensive inspection plan and checklists. This meticulous process aims to enhance quality assurance without the involvement of automation.
Problem:
Our faced challenges in efficiently managing the inspection plan creation process manually. The customer needed to invest a considerable number of man-hours to execute the process. Furthermore, it led to potential delays in creating inspection plans, difficulties in consistently comparing articles with standard parts and challenges in maintaining thorough checklists. These inefficiencies hindered the company's ability to ensure precision and quality in manufacturing processes, impacting overall product quality and customer satisfaction.
Solution:
Recognizing the need to enhance their Inspection Plan Creation process, we adopted a systematic approach to improve accuracy and efficiency. Our key solutions included:
1. Detailed Drawing and Specification Analysis: We initiated a manual process to obtain detailed drawings and specifications for articles, ensuring a comprehensive understanding of the manufacturing requirements.
2. Thorough Article Analysis: Despite manual processing, our dedicated team analyzed articles by comparing them with standard parts, ensuring a meticulous examination for quality benchmarks.
3. Parameter Devising: By actively devising major attributes and parameters to be checked, we ensured consistency in quality criteria and precision benchmarks.
4. Comprehensive Inspection Plan Creation: We meticulously created a comprehensive inspection plan and checklists, incorporating major attributes and parameters to guide the inspection process thoroughly.
Results:
The changes implemented in the Inspection Plan Creation process led to significant improvements in precision and quality assurance for Würth Industrie Service GmbH & Co. KG. The key results included:
1. Efficient Inspection Plan Creation: Despite manual processes, the time taken to create inspection plans decreased considerably, ensuring quicker adaptation to changing manufacturing requirements.
2. Improved Article Analysis: Meticulous article analysis led to an increase in precision, reducing errors in comparing articles with standard parts and enhancing overall quality assurance.
3. Consistent Parameter Checking: The active devising of major attributes and parameters resulted in an increase in consistency, ensuring uniformity in quality criteria and precision benchmarks.
4. Enhanced Quality Assurance: The comprehensive inspection plan creation process led to an improvement in overall quality assurance, positively impacting product quality and customer satisfaction.
5. Time Saving: Our approach led to significant time savings per month. We saved considerable hours for our customer in a month. This saved time can be utilized for executing different core operations.
Conclusion:
By transferring the Inspection Plan Creation process, our customer accelerated the physical inspection process with precision and quality assurance. By implementing detailed drawing and specification analysis, thorough article analysis, parameter devising and comprehensive inspection plan creation, we successfully improved precision and quality assurance. The results underscore the value of manual processes in ensuring the meticulous creation of inspection plans and checklists.