Purchasing
Sales Operations
Product Article Master
Logistics
Finance
- Accounts Payable
- Invoice verification & posting invoices
- Making payments to vendors & queries
- Goods receipt and invoice receipt clearance
- Analyze vendor open line items
- Overhead cost invoices
- MIRO Posting
- Accounts Recievables
- Scheduling a dunning run
- Settling customer payments & queries
- Self-billing of customer’s invoice
- Bank reconciliation
- Customer Invoice Clearance
- Sales Order Booking
- Daily Credit Run
- Releasing Green Orders
Market Research
Chemical Master Data Update

Würth Business Services handles the article data management operations related to the Product Article Master Department. We handle a wide range of processes for maintaining the accurate and standardized article data through SAP system. Our Team utilizes the advanced tools and software, implements standard procedures, maintains quality standards, and efficiently manages and maintains the article data.
Among many processes, Chemical Master Data Update is one of the processes handled by us. In this process, we carry out maintenance and upload of data in the Enterprise Resource Planning (ERP) system. Once an Excel sheet containing article numbers is received from customers, we find the missing attributes for articles using the Sicherheitsdatenblatt (SDB), which implies Safety Database, from supplier’s website and fill up the data. We also utilize Robotic Process Automation (RPA) for uploading SBD.
Work Flow
WORK FLOW OF THE PROCESS
01. Find
Find current SDB from supplier’s website for article number
02. Send
Send the current SDB to RPA to upload in ERP system
03. Carry
Carry out attribute check of the current SDB in ERP system
04. Inform
Inform the customers once attribute check is done
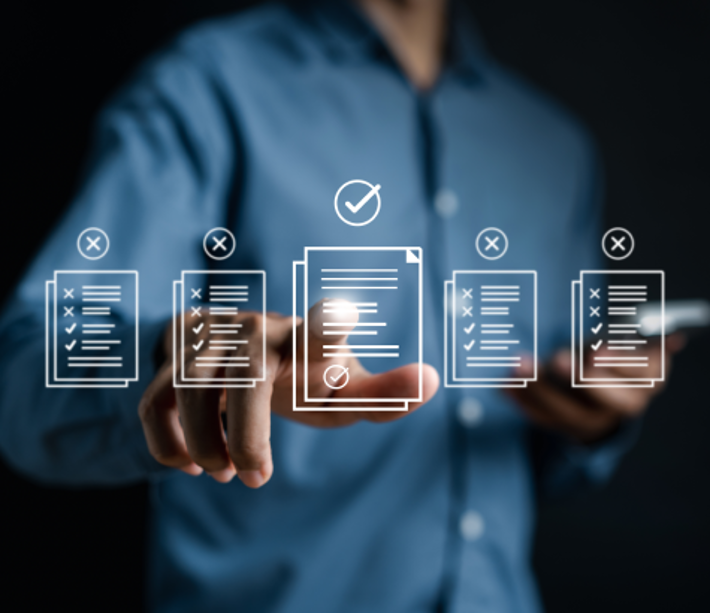
Benefits
Value-added
BENEFITS OF OUR CUSTOMERS
☞ Choose the right supplier with products possessing right safety parameters
☞ Easy access for Sales Teams to generate an offer and sell the articles
☞ Decide whether to keep an article at warehouse based on safety
☞ Avail the information about dangerous articles easily in the system
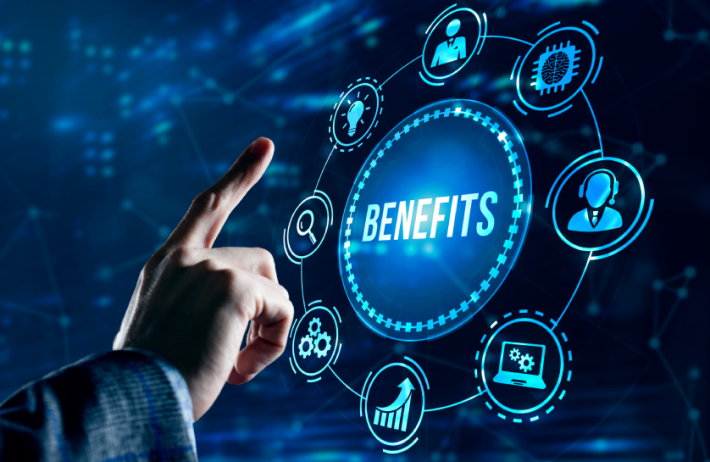
Transition
TIME TAKEN FOR TRANSITION
Step 1
Analysis of requirements – 1 Week
Step 2
Resource planning – 1 Day
Step 3
Tools requirement planning – 3 Days
Step 4
Training/Documentation – 2 Days
Step 5
Trial submission – 5 Days
Step 6
Transfer – 5 Days
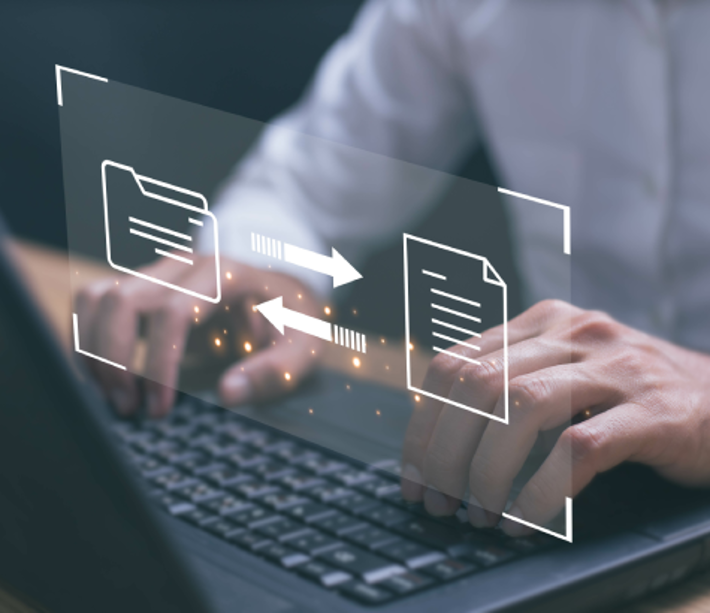
Case study:
Streamlining Chemical Master Data Update Process for Enhanced Data Integrity
Introduction:
Accurate and up-to-date chemical master data is critical for ensuring regulatory compliance and safety. Our customer, Würth Industrie Service GmbH & Co. KG, recognized the need to maintain chemical master data to ensure data integrity. This case study explores the Chemical Master Data Update process, where a dedicated team finds the current Safety Database (SDB) from the supplier's website, sends the SDB to Robotic Process Automation (RPA) for uploading into the ERP system, conducts an attribute check of the current SDB in the ERP system and informs customers once the attribute check is complete. This meticulous process aims to maintain data integrity without the involvement of automation.
Problem:
Our customer encountered challenges in effectively managing chemical master data updates manually. The customer needed to invest a considerable number of man-hours to execute the process. Furthermore, it led to potential errors in data entry, delays in updating safety data sheets and difficulties in maintaining consistent data attributes. These inefficiencies hindered the company's ability to ensure regulatory compliance, resulting in potential safety risks and data discrepancies. This impacted overall data management efficiency.
Solution:
Recognizing the need to enhance their Chemical Master Data Update process, we adopted a systematic approach to improve accuracy and order processing efficiency. Our key solutions included:
1. Comprehensive SDB Retrieval: We initiated a manual process to find the current Safety Data Sheet (SDB) from the supplier's website, ensuring a comprehensive approach to data retrieval.
2. RPA Collaboration for ERP Upload: Despite manual processing, our dedicated team collaborated with Robotic Process Automation (RPA) to upload the current SDB into the ERP system, leveraging automation for this specific task.
3. Attribute Check in ERP System: We actively conducted an attribute check of the current SDB in the ERP system, ensuring consistency and accuracy in data attributes related to chemical master data.
4. Customer Notification: Meticulously informing customers once the attribute check was complete, the company demonstrated transparency in data management processes.
Results:
The changes implemented in the Chemical Master Data Update process led to significant improvements in data integrity and efficiency for Würth Industrie Service GmbH & Co. KG. The key results included:
1. Efficient Data Updates: By leveraging RPA for ERP upload, we reduced the time taken to update safety data sheets, ensuring timely compliance with regulatory requirements.
2. Data Accuracy Improvement: Despite manual attribute checks, data accuracy improved considerably, reducing errors in chemical master data and enhancing overall data integrity.
3. Enhanced Customer Communication: Timely customer notifications resulted in an increase in customer satisfaction, demonstrating the commitment to keeping customers informed about data updates.
4. Time Saving: Our approach led to significant time savings per month. We saved nearly 42 hours for our customer in a month. This saved time can be utilized for executing different core operations.
Conclusion:
By transferring the Chemical Master Data Update process, our customer maintained data integrity and regulatory compliance. By implementing comprehensive SDB retrieval, RPA collaboration, manual attribute checks and proactive customer notifications, we successfully improved data management efficiency and customer satisfaction. The results underscore the value of combining manual and automated processes to ensure accurate and up-to-date chemical master data.