Purchasing
Sales Operations
Product Article Master
Logistics
Finance
- Accounts Payable
- Invoice verification & posting invoices
- Making payments to vendors & queries
- Goods receipt and invoice receipt clearance
- Analyze vendor open line items
- Overhead cost invoices
- MIRO Posting
- Accounts Recievables
- Scheduling a dunning run
- Settling customer payments & queries
- Self-billing of customer’s invoice
- Bank reconciliation
- Customer Invoice Clearance
- Sales Order Booking
- Daily Credit Run
- Releasing Green Orders
Market Research
Material Requirement Planning (MRP)
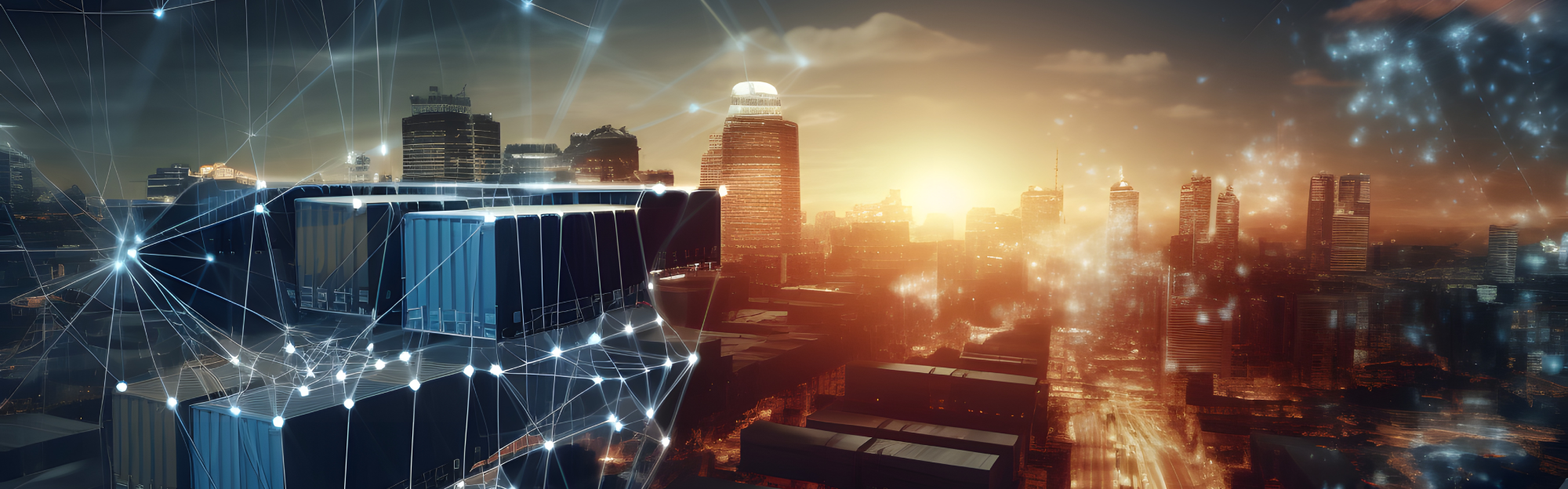
The Purchasing Department of Würth Business Services is equipped with a team of highly experienced procurement and purchasing professionals. We are instrumental in fulfilling the business-specific requirements by handling different processes related to Purchasing and serving customers across the globe. Among many non-core procurement and Purchasing-related processes handled by us, Material Requirement Planning is one of the major processes.
In this process, we plan and place purchase orders as per the requirement of the customer. During planning stages, the tool determines the appropriate time and price for placing an order. We handle the end-to-end process from planning and negotiating to placing orders and taking follow-ups for on-time delivery. In this way, the tool helps businesses in making smart decisions and saving costs. Below is the work flow of this process.
Work Flow
WORK FLOW OF THE PROCESS
01. Plan
Plan as per the requirements of customers
02. Negotiate
Negotiate prices with different suppliers
03. Place
Place the purchase order or draft a contract
04. Take
Take follow-ups with the supplier for timely deliveries
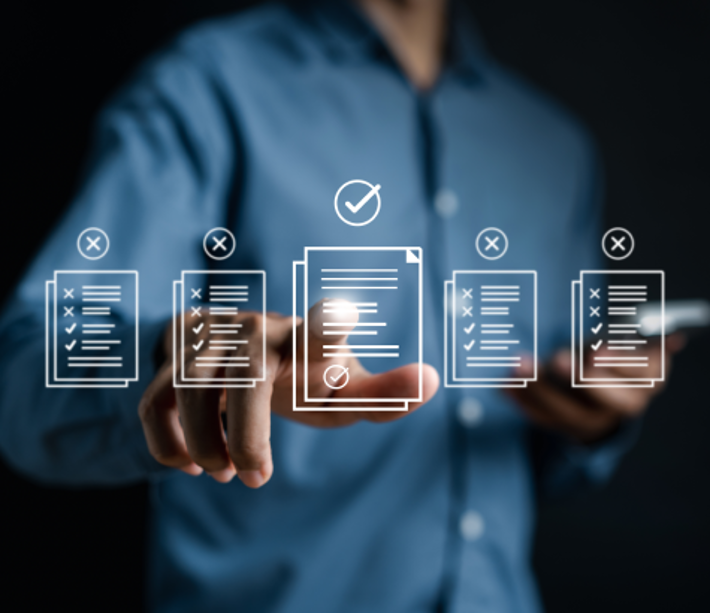
Benefits
Value-added
BENEFITS OF OUR CUSTOMERS
☞ Balance supply and demand to fulfil customer requirements
☞ Save costs by opting for the most suitable supplier
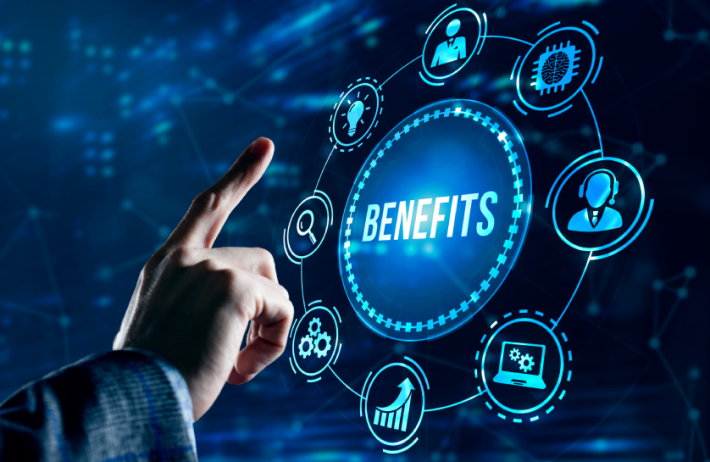
Transition
TIME TAKEN FOR TRANSITION
Step 1
Analysis of requirements – 1 Week
Step 2
Documentation – 2 Weeks
Step 3
Create framework – 3 Week
Step 4
Step-by-step implementation – 4 Weeks
Step 5
Transfer – 2 Weeks
For more assistance in understanding the transition process, kindly get in touch with us at contact-wbs@wuerth-industrie.com
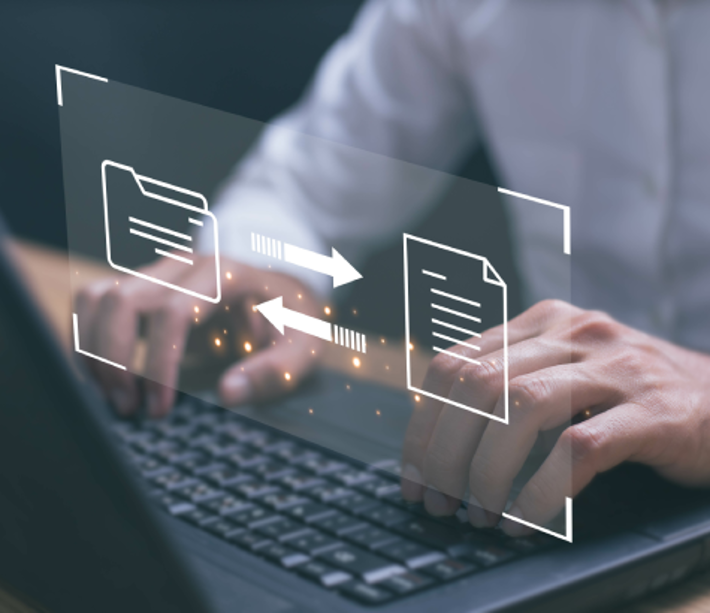
Case study:
Implementing Material Requirement Planning for Effective Procurement Management
Introduction:
In the landscape of modern business, efficient procurement management is vital for maintaining seamless operations and optimizing costs. Our customer, Würth Canada Ltd., recognized the significance of Material Requirement Planning (MRP) process to plan and place purchase orders as per the requirement. By utilizing a comprehensive tool that aids in decision-making, negotiation, order placement, and follow-up, we aim to enhance procurement efficiency and cost savings.
Problem:
Our customer faced challenges in effectively managing their procurement process, which often led to inefficiencies, missed deadlines, overstocking, and suboptimal purchasing decisions. The absence of an organized approach to acquire the material as per requirement led to unnecessary costs, delays in delivery, and difficulties in maintaining customer satisfaction.
Solution:
Recognizing the need to improve their Material Requirement Planning process, we undertook the task of streamlining their procurement operations and enhance decision-making. We implemented a comprehensive tool that aided in the entire MRP process. This tool facilitated knowing the optimal times for order placement, considering factors, such as lead times, production schedules, and customer demand. It also enabled effective price negotiations based on market conditions and historical data.
Our tool facilitated the handling of the entire procurement process seamlessly, from planning and negotiating to order placement and follow-up for on-time delivery. This holistic approach ensured that every step of the process was carefully monitored and managed to avoid any potential discrepancies.
Results:
The implementation of the MRP process yielded significant improvements in procurement management and cost efficiency. Key results included:
1. Optimized Procurement Decisions: Utilizing the planning tool resulted in an improvement in procurement decisions, leading to better timing for order placement and improved negotiation outcomes.
2. Timely Deliveries: With a focused follow-up approach enabled by the tool, the company achieved a reduction in delivery delays. This positively impacted customer satisfaction and reduced the risk of operational disruptions.
3. Cost Savings: The comprehensive planning tool contributed to a reduction in procurement costs due to better negotiation outcomes and improved inventory management.
4. Time Savings: By transferring the MRP process, our customer was able to focus on core operations. By carrying out effective planning and implementing a tool, we saved nearly 165.32 hours for our customer in a month.
Conclusion:
This case study highlights the significance of manual Material Requirement Planning in achieving efficient procurement management and cost optimization. By leveraging a comprehensive tool that aids in decision-making, negotiation, order placement, and follow-up, our customer, Würth Canada Ltd., successfully improved procurement accuracy, timeliness, and cost-effectiveness. A well-executed MRP process led to effective procurement practices and overall business success.