Purchasing
Sales Operations
Product Article Master
Logistics
Finance
- Accounts Payable
- Invoice verification & posting invoices
- Making payments to vendors & queries
- Goods receipt and invoice receipt clearance
- Analyze vendor open line items
- Overhead cost invoices
- MIRO Posting
- Accounts Recievables
- Scheduling a dunning run
- Settling customer payments & queries
- Self-billing of customer’s invoice
- Bank reconciliation
- Customer Invoice Clearance
- Daily Credit Run
- Releasing Green Orders
Market Research
Releasing Green Orders
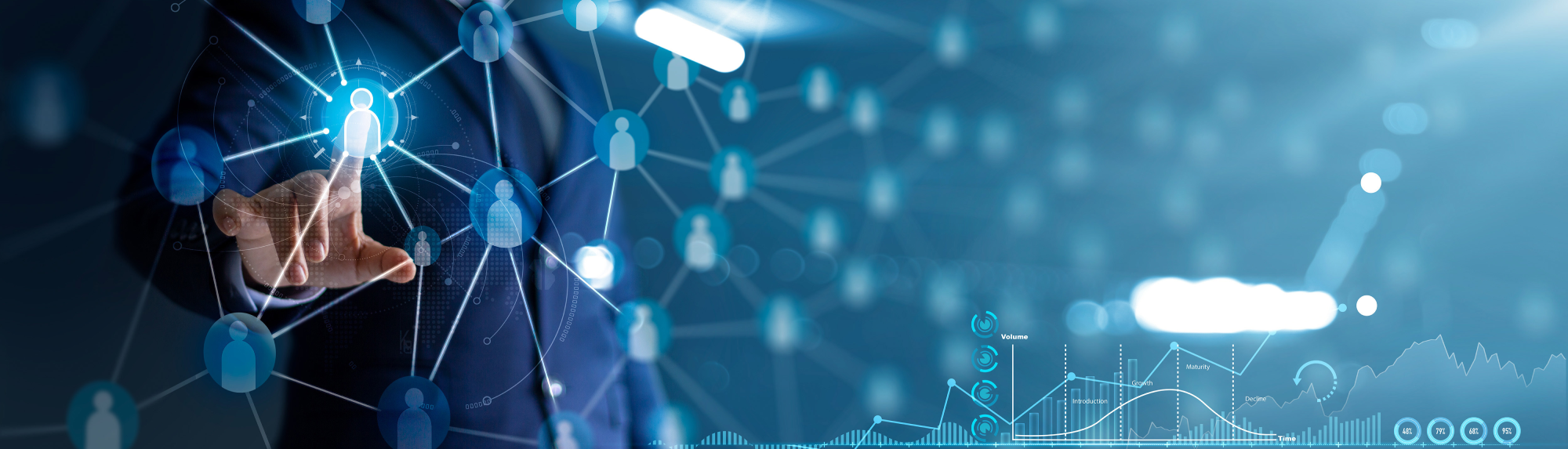
Würth Business Services handles the non-core financial operations to support the Finance Teams of companies within the Würth Group. Our Team ensures that companies maintain error-free and detailed accounting records, settle payments on a timely basis, carry out effective vendor management, and speed up the accounting processes. We handle different processes under the Accounts Payable and Accounts Receivable portfolio.
Among different processes we handle under the Accounts Receivable portfolio, Releasing Green Orders is one of them. In this process, our team manually checks whether we have received the payments for customer orders that have been blocked. These orders are blocked in the Enterprise Resource Planning (ERP) system as we have not received the payment for older invoices. Once we receive the payment for older invoices, the customer orders will be released.
Work Flow
WORK FLOW OF THE PROCESS
01. Check
Check the orders marked in Red, Yellow and Green in the ERP system
02. Select
Select all the orders which are marked in Green
03. Click
Click on Release button to release these order
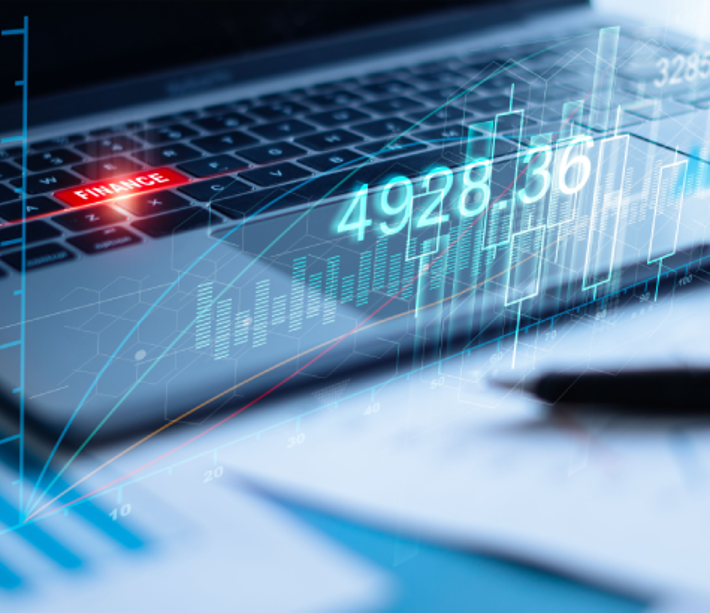
Benefits
Value-added
BENEFITS OF OUR CUSTOMERS
☞ Save time in releasing the orders upon receiving payments for older invoices
☞ Ensure smooth accounting processes with precision
☞ Focus on core operations
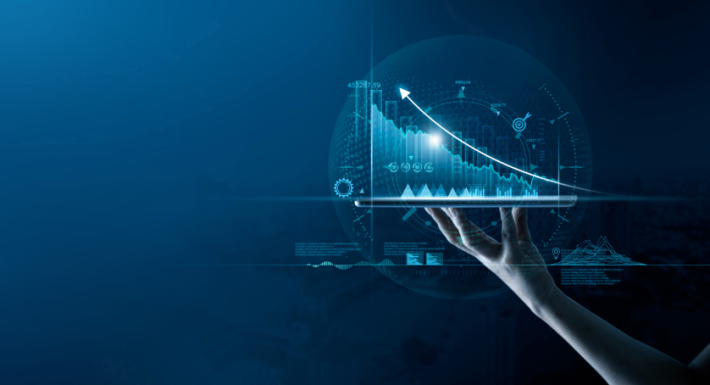
Transition
TIME TAKEN FOR TRANSITION
Step 1
Analysis of requirements – 1 Week
Step 2
Documentation – 1-2 Weeks
Step 3
Create framework – 1 Week
Step 4
Step-by-step implementation – 2 Weeks
Step 5
Transfer – 1 Week
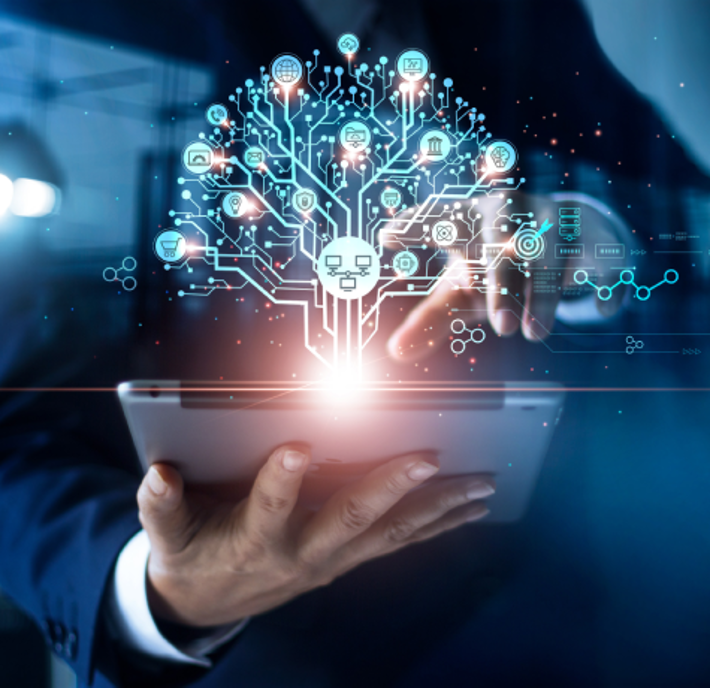
Case study:
Streamlining Green Order Release Process for Improved Order Fulfillment
Introduction:
Efficient order processing is essential for meeting customer demands and maintaining a smooth financial operations. Our customer, Würth België N.V., recognized the need to ensure orders have been released after payments are received. This case study explores the manual Releasing Green Orders process, in which our dedicated team checks orders marked in Red, Yellow, and Green in the ERP system, selects all orders marked in Green and manually clicks on the Release button to facilitate order release. This meticulous process aims to optimize order fulfillment.
Problem:
The company encountered challenges in effectively releasing orders marked in Green manually. he customer needed to invest a considerable number of man-hours to execute the process. Furthermore, it led to potential errors in order identification, delays in order release and difficulties in maintaining a streamlined order fulfillment process. These inefficiencies hindered the company's ability to process orders swiftly, resulting in delays in customer deliveries and potential customer dissatisfaction. This impacted overall order fulfillment efficiency.
Solution:
Recognizing the need to enhance their Releasing Green Orders process, we adopted a systematic approach to improve accuracy and order processing efficiency. Our key solutions included:
1. Order Identification: We initiated a manual process to check orders marked in Red, Yellow, and Green in the ERP system, ensuring accurate identification of orders to be released.
2. Efficient Order Selection: Despite manual processing, our dedicated team selected all orders marked in Green with precision, avoiding errors in order selection.
3. Manual Release: We actively clicked on the Release button for the selected Green orders, ensuring timely order release without the involvement of automation.
Results:
The changes implemented in the Releasing Green Orders process led to significant improvements in order processing efficiency and accuracy for Würth België N.V. The key results included:
1. Order Fulfillment Efficiency: By implementing efficient order identification and selection, we reduced the time spent on order release considerably, ensuring swift and accurate order fulfillment.
2. Data Accuracy Improvement: Despite manual processes, data accuracy improved significantly, reducing errors in order release and enhancing overall order processing precision.
3. Improved Customer Satisfaction: Efficient order release resulted in an increase in on-time deliveries, leading to improved customer satisfaction and strengthened customer relationships.
4. Time Saving: Our approach led to significant time savings per month. We saved nearly 14 hours for our customer in a month. This saved time can be utilized for executing different core operations.
Conclusion:
By transferring the MIRO Posting process, our customer ensured streamlined order release processes for improved order fulfillment and enhanced customer satisfaction. By implementing efficient order identification, selection, and manual release, the company successfully improved order processing efficiency and customer relations. The results highlight the value of a well-executed Releasing Green Orders process in maintaining effective order operations and delivering timely and accurate order releases.