Purchasing
Sales Operations
Product Article Master
Logistics
Finance
- Accounts Payable
- Invoice verification & posting invoices
- Making payments to vendors & queries
- Goods receipt and invoice receipt clearance
- Analyze vendor open line items
- Overhead cost invoices
- MIRO Posting
- Accounts Recievables
- Scheduling a dunning run
- Settling customer payments & queries
- Self-billing of customer’s invoice
- Bank reconciliation
- Customer Invoice Clearance
- Sales Order Booking
- Daily Credit Run
- Releasing Green Orders
Market Research
COMPLAINT MANAGEMENT FOR INCOMING GOODS DEPARTMENT
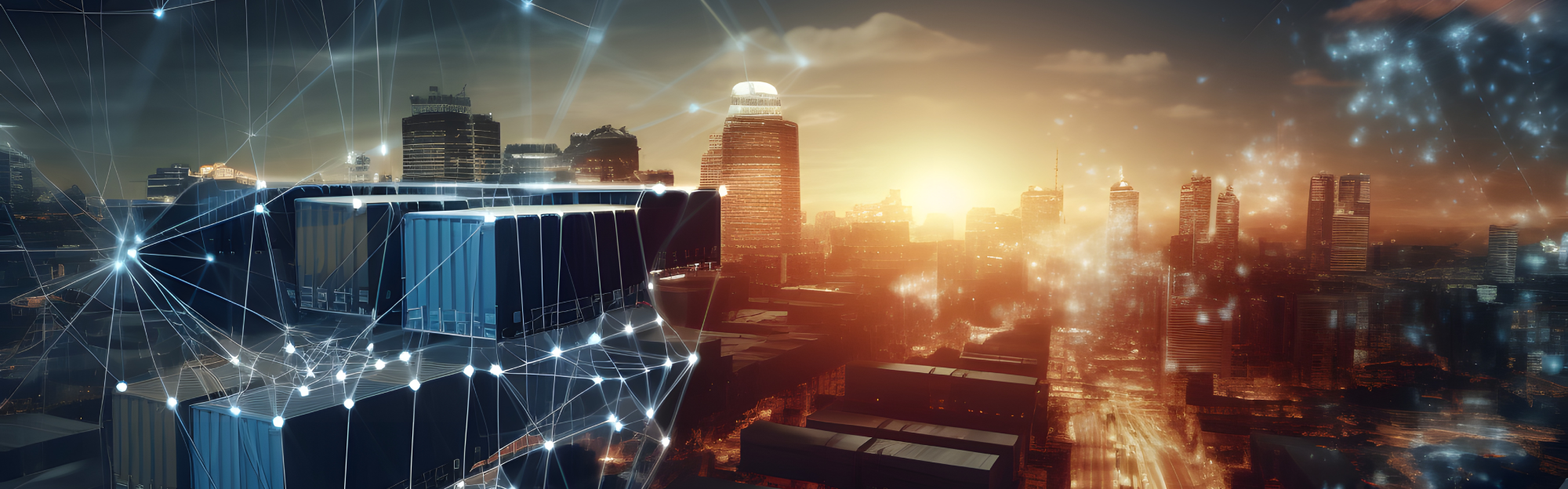
The Purchasing Department of Würth Business Services is equipped with a team of highly experienced procurement and purchasing professionals. We are instrumental in fulfilling the business-specific requirements by handling different processes related to Purchasing and serving customers across the globe. Among many non-core procurement and Purchasing-related processes handled by us, Complaint Management for Incoming Goods Department is one of the major processes.
In this process, our team collaborates with suppliers, purchasers and colleagues from Würth Group companies for solving the complaints regarding incoming goods. We process and close the complaints effectively using the Enterprise Resource Planning (ERP) and emails. We also reviewing the 8D reports with details and answer the technical queries of suppliers with relevant standards.
Work Flow
WORK FLOW OF THE PROCESS
01. Receive
Receive complaints about non-conformities and defects about incoming goods
02. Process
Process the complaints through ERP with defect protocol and inspection reports
03. Receive
Receive the 8D report with necessary corrective and preventive actions to avoid the recurrence
04. Review
Review the received inspection reports as per the standards and norm requirements
05. Verify
Verify 8D report with mentioned suitable actions relevant to defects
06. Follow
Follow up with suppliers with terms and negotiations to take decisions on acceptance and rejection of goods
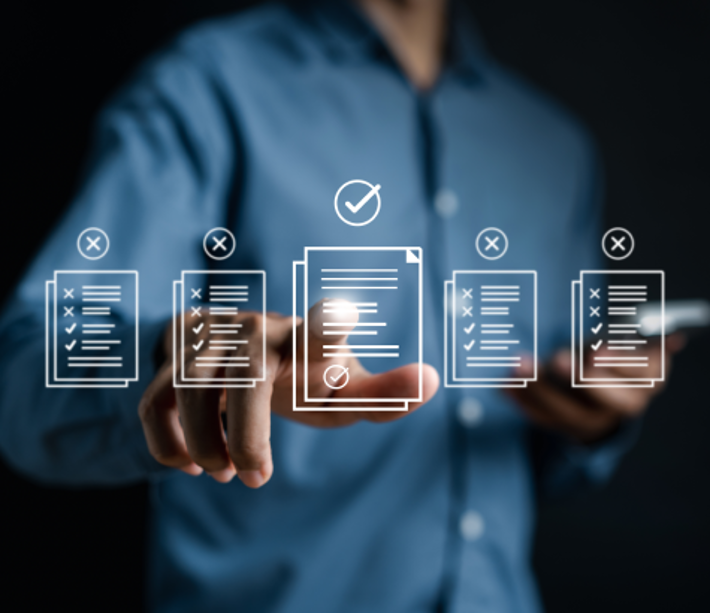
Benefits
Value-added
BENEFITS OF OUR CUSTOMERS
☞Resolve quality-related issues and reduce the workload with our technical proficiency
☞Technical guidance for the implementation of quality systems for suppliers
☞Improve customer satisfaction with streamlined complaint management
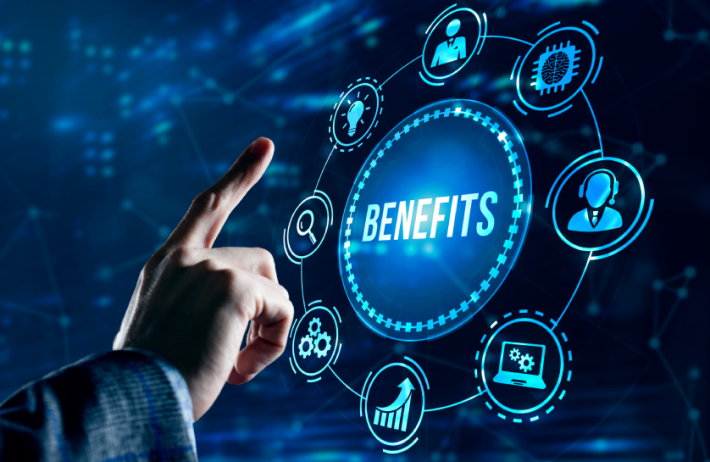
Transition
TIME TAKEN FOR TRANSITION
Step 1
Analysis of requirements – 1 Week
Step 2
Documentation – 1-2 Weeks
Step 3
Create framework – 1 Week
Step 4
Step-by-step implementation – 2 Weeks
Step 5
Transfer – 1 Week
For more assistance in understanding the transition process, kindly get in touch with us at contact-wbs@wuerth-industrie.com
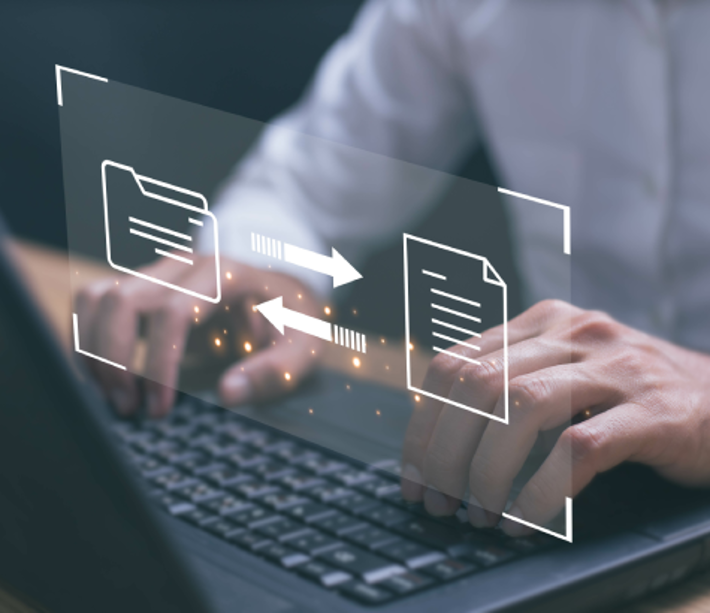
Case study:
Enhancing Complaint Management Process for Incoming Goods
Introduction:
Managing complaints in the Incoming Goods Department is vital to ensuring the integrity and conformity of materials received. Our customer, Würth Industrie Service GmbH & Co. KG, recognized the need to handle and manage these complaints to build strong customer relationships and improve efficiency. This case study delves into the Complaint Management for Incoming Goods Department process, in which our team receives complaints about non-conformities and defects in incoming goods, processes the complaints through ERP with defect protocols and inspection reports and receives 8D reports with corrective and preventive actions. Then we review inspection reports as per standards, verify 8D reports, and tale follow-ups with suppliers for decisions on acceptance or rejection of goods. This meticulous process aims to strengthen quality control without the involvement of automation.
Problem:
Our customer faced challenges in efficiently managing the Complaint Management process. The customer needed to invest a considerable number of man-hours to execute the process. Furthermore, it led to potential delays in processing complaints, difficulties in consistently reviewing inspection reports and challenges in tracking and verifying corrective & preventive actions. These inefficiencies hindered the customer's ability to ensure robust quality assurance in incoming goods, impacting overall production quality and customer satisfaction.
Solution:
Recognizing the need to enhance their Complaint Management process, we adopted a systematic approach to improve accuracy and order processing efficiency. Our key solutions included:
1. Efficient Complaint Processing: We initiated a manual process to receive complaints about non-conformities and defects, ensuring a systematic approach to logging and processing each complaint through the ERP system with defect protocols.
2. Comprehensive 8D Reports: Despite manual processing, our dedicated team ensured comprehensive 8D reports with necessary corrective and preventive actions to avoid recurrence, fostering a proactive approach to quality issues.
3. Thorough Inspection Report Reviews: By actively reviewing received inspection reports as per standards and norm requirements, we implemented meticulous examination to identify non-conformities and defects.
4. Verification of Corrective Actions: We implemented a thorough verification process, comparing the received 8D reports with mentioned suitable actions relevant to defects. This ensured alignment with quality standards.
5. Effective Supplier Communication: Proactively following up with suppliers, we engaged in terms and negotiations to make informed decisions on the acceptance or rejection of goods, fostering collaboration for continuous improvement.
Results:
The changes implemented in the Complaint Management process led to significant improvements in quality assurance and incoming goods control for Würth Industrie Service GmbH & Co. KG. The key results included:
1. Streamlined Complaint Processing: Despite manual processes, the time taken to process complaints decreased considerably, ensuring quicker responses to quality issues and improved overall quality control.
2. Enhanced Corrective Action Verification: Meticulous verification of corrective actions resulted in an increase in accuracy, reducing errors in aligning 8D reports with defect protocols.
3. Improved Supplier Collaboration: Proactive communication with suppliers led to an improvement in supplier collaboration, creating a conducive environment for quality improvements and mutual understanding.
4. Strengthened Quality Assurance: The comprehensive approach to Complaint Management resulted in an enhancement in overall quality assurance, positively impacting production quality and customer satisfaction.
5. Time Saving: Our approach led to significant time savings per month. We saved considerable hours for our customer in a month. This saved time can be utilized for executing different core operations.
Conclusion:
By transferring the Complaint Management for Incoming Goods Department process, our customer ensured that complaints were managed efficiently. By implementing efficient complaint processing, comprehensive 8D reports, thorough inspection report reviews, verification of corrective actions and effective supplier communication, we successfully helped in improving the quality. The results highlight the value of manual processes in ensuring meticulous handling of non-conformities and defects.