Purchasing
Sales Operations
Product Article Master
Logistics
Finance
- Accounts Payable
- Invoice verification & posting invoices
- Making payments to vendors & queries
- Goods receipt and invoice receipt clearance
- Analyze vendor open line items
- Overhead cost invoices
- MIRO Posting
- Accounts Recievables
- Scheduling a dunning run
- Settling customer payments & queries
- Self-billing of customer’s invoice
- Bank reconciliation
- Customer Invoice Clearance
- Sales Order Booking
- Daily Credit Run
- Releasing Green Orders
Market Research
Drop Shipment Order Processing
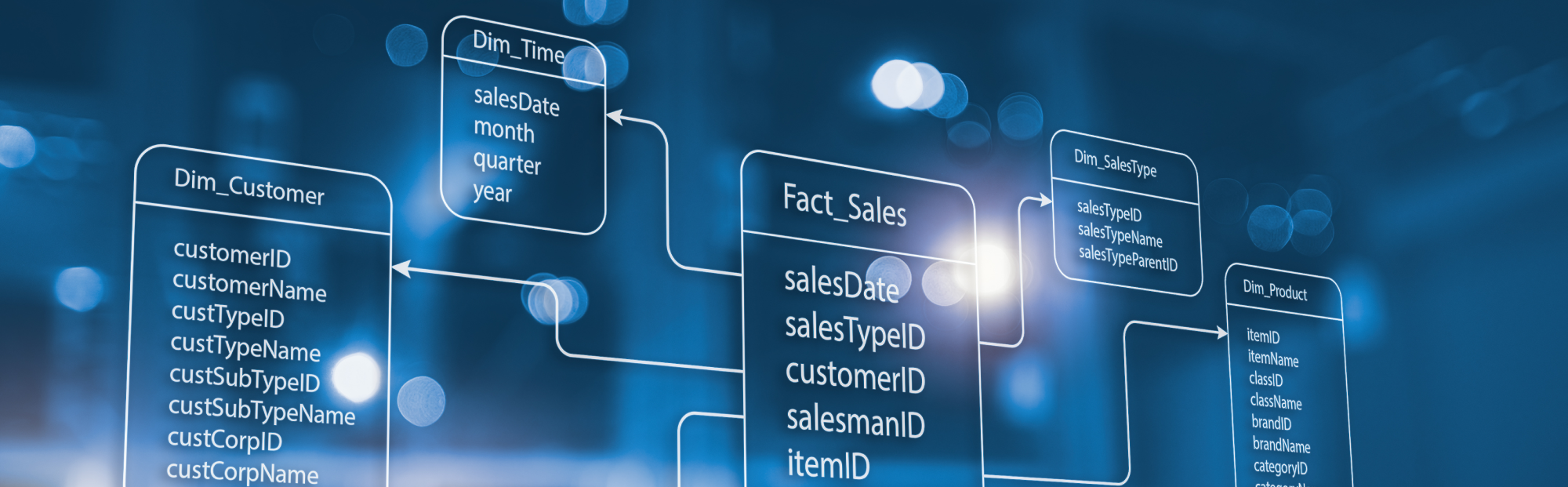
Würth Business Services handles the non-core Sales Operations to support your Sales Team in achieving the targets and registering a significant business growth. We handle many processes to help your business accelerate the Sales and Operations Planning (S&OP) tasks. Our services are aimed at driving profitability and providing rapid solutions.
Among many processes we handle, Drop Shipment Order Processing is one of the processes. In this process, a customer places the order for filling up Kanban containers installed at their manufacturing plants. Then the customer selects the Würth-approved drop shipment supplier. If the order is not delivered within the given deadline, our team takes updates from the suppliers. We check the delivery dates of the previous day and determine the current status of the order through Kanban Management System (KMS). If the status shows that the drop shipment order is pending for delivery, we send emails to the supplier to understand the reasons for delay. Based on their responses, we reply to their responses and update the details in KMS.
Work Flow
WORK FLOW OF THE PROCESS
01. Extract
Extract a list of backlog articles from KMS
02. Determine
Determine the supplier and send reminders for backlogs
03. Receive
Receive a response and update the remarks in KMS
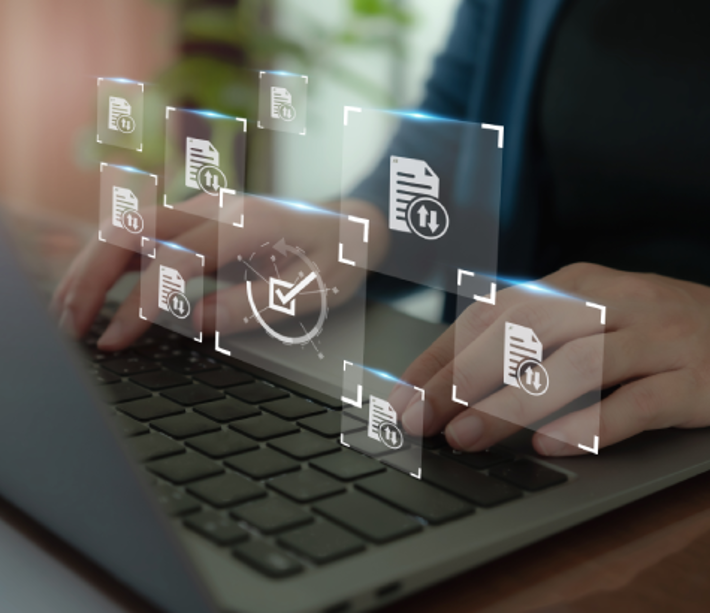
Benefits
Value-added
BENEFITS OF OUR CUSTOMERS
☞ Send reminders to suppliers to avail backlog orders
☞ Stay updated about the current status of backlog orders
☞ Maintain strong relationships with suppliers
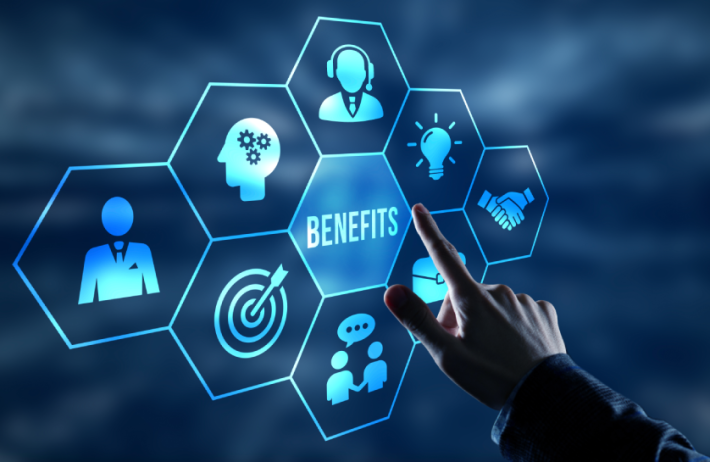
Transition
TIME TAKEN FOR TRANSITION
Step 1
Analysis of customer requirements – 1 Working Day
Step 2
Resource planning – 2 Working Days
Step 3
Tools requirement – 2 Working Days
Step 4
Training phase/Documentation – 1 Working Day
Step 5
Trial submission – 5 Working Days
Step 6
Transfer – 6 Working Days
For more assistance in understanding the transition process, kindly get in touch with us at contact-wbs@wuerth-industrie.com
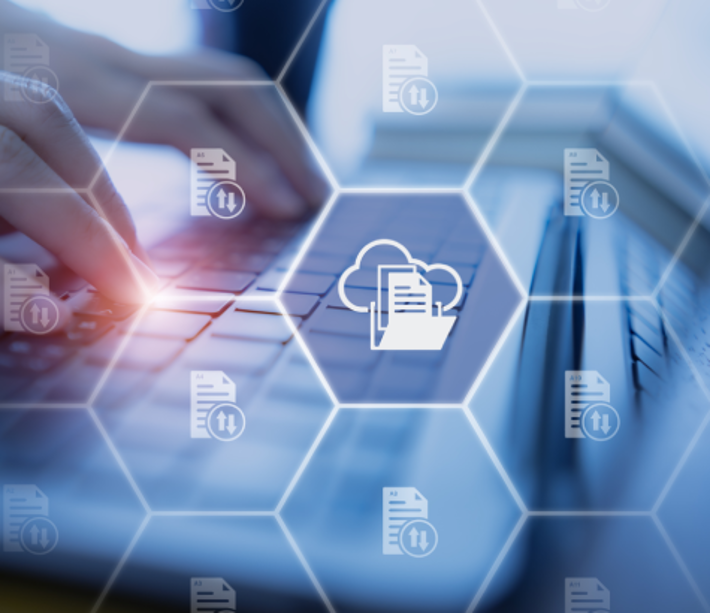
Case study:
Optimizing Drop Shipment Order Processing for Enhanced Customer Satisfaction
Introduction:
In the landscape of supply chain management, efficient drop shipment order processing is essential for meeting customer demands and maintaining satisfaction. Our customer, Würth Industrie Service GmbH & Co. KG, recognized the need to take follow-ups for backlog of orders with drop shipment supplier. This case study delves into the Drop Shipment Order Processing process, in which customers need Kanban containers to be filled at their manufacturing plants. The process involves selecting Würth-approved drop shipment suppliers, monitoring order delivery deadlines and proactively addressing delays through communication with suppliers.
Problem:
Our customer faced challenges in effectively managing the Drop Shipment Order Processing process manually. The customer needed to invest a considerable number of man-hours to execute the process. Furthermore, there were inefficiencies in monitoring order status, tracking delivery deadlines and addressing delays promptly. This led to potential delays in fulfilling customer orders, impacting customer satisfaction and trust in the company's services.
Solution:
Recognizing the need to speed up Drop Shipment Order Processing, we implemented a series of solutions to streamline the manual process and enhance customer satisfaction. Our key solutions included:
1. Improved Monitoring and Communication: We implemented a systematic approach to monitor order delivery deadlines using the Kanban Management System (KMS). Proactive communication with suppliers was established to address any potential delays promptly.
2. Timely Follow-Up and Resolution: Upon identifying delays through KMS, we initiated timely follow-ups with suppliers to understand the reasons for delays. Clear communication and resolution plans were established to mitigate delays and ensure timely order fulfillment.
Results:
The improvements made to the Drop Shipment Order Processing process yielded significant results, enhancing overall efficiency and customer satisfaction for Würth Industrie Service GmbH & Co. KG. The key results included:
1. Reduced Order Delays: By implementing proactive monitoring and communication, order delays were reduced and timely delivery of Kanban containers to customers' manufacturing plants was possible.
2. Enhanced Supplier Collaboration: Clear communication channels and proactive follow-ups improved collaboration with suppliers, resulting in a decrease in response time to address delays and resolve issues.
3. Improved Customer Satisfaction: The streamlined process and timely resolution of delays contributed to a increase in customer satisfaction ratings, enhancing the company's reputation for reliable and efficient service.
4. Time Saving: Our approach led to significant time savings per month. We saved nearly 38 hours for our customer in a month. This saved time can be utilized for executing different core operations.
Conclusion:
By transferring the Drop Shipment Order Processing process, our customer optimized the process to ensure timely and efficient order fulfillment. By implementing proactive monitoring and timely communication & resolution strategies, we successfully mitigated delays and improved customer satisfaction. With meticulous manual execution, this process can significantly enhance supply chain efficiency and customer experience.