Purchasing
Sales Operations
Product Article Master
Logistics
Finance
- Accounts Payable
- Invoice verification & posting invoices
- Making payments to vendors & queries
- Goods receipt and invoice receipt clearance
- Analyze vendor open line items
- Overhead cost invoices
- MIRO Posting
- Accounts Recievables
- Scheduling a dunning run
- Settling customer payments & queries
- Self-billing of customer’s invoice
- Bank reconciliation
- Customer Invoice Clearance
- Sales Order Booking
- Daily Credit Run
- Releasing Green Orders
Market Research
Expediting
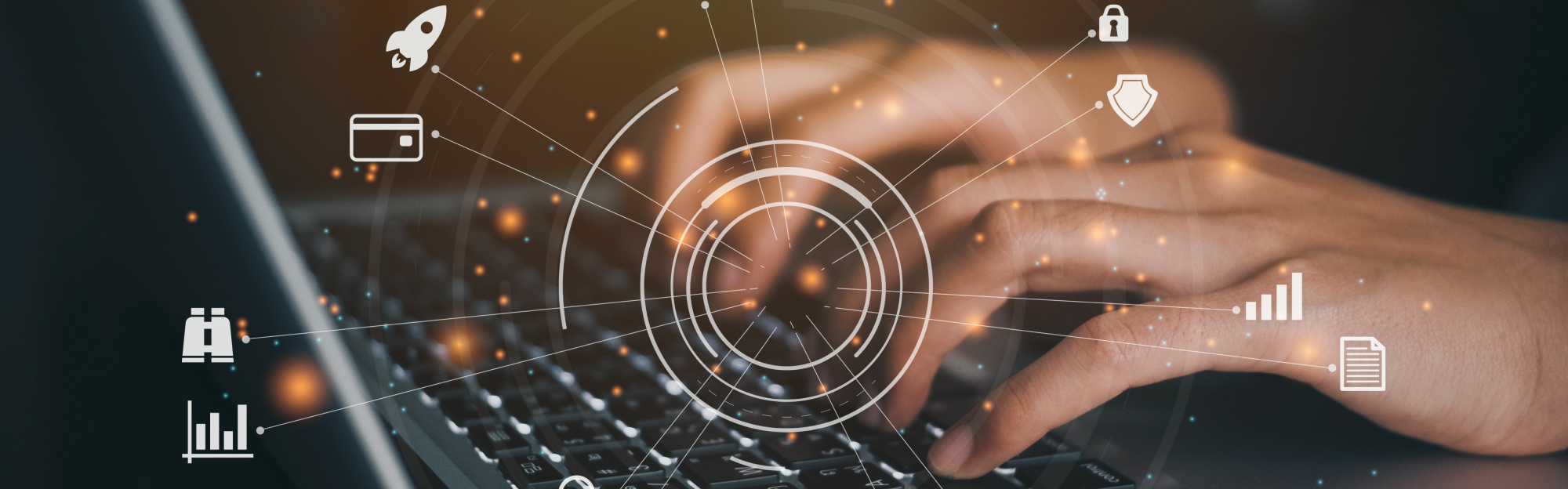
The Purchasing Department of Würth Business Services is equipped with a team of highly experienced procurement and purchasing professionals. We are instrumental in fulfilling the business-specific requirements by handling different processes related to Purchasing and serving customers across the globe. Among many non-core procurement and Purchasing-related processes handled by us, Expediting is one of the major processes.
In this process, we take follow-ups regarding the pending quotations from the supplier. If there are delays from the suppliers, we take updates regarding the Estimated Time of Arrival (ETA) and store the data in the ERP system. Below is the work flow of this process.
Work Flow
WORK FLOW OF THE PROCESS
01. Send
Send emails to the suppliers for order confirmation
02. Determine
Determine ETA based on reply from suppliers
03. Enter
Enter the updated data in the ERP system
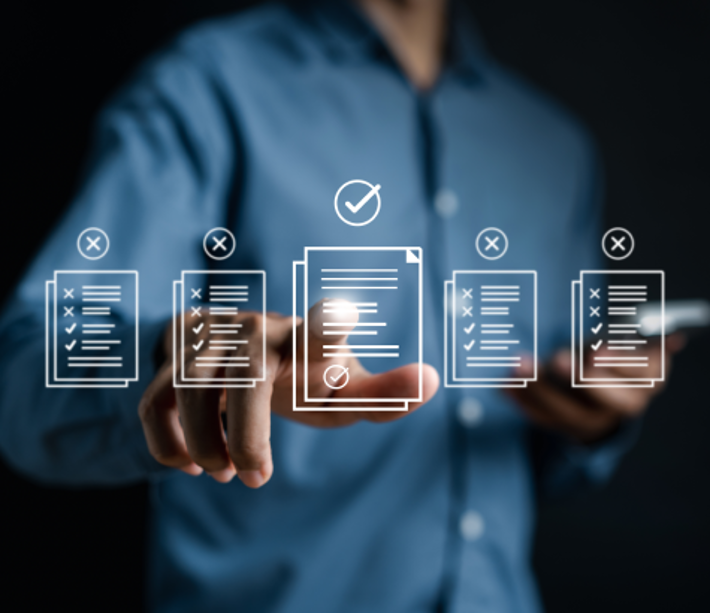
Benefits
Value-added
BENEFITS OF OUR CUSTOMERS
☞ Ensure timely order confirmation
☞ Determine ETA and develop further schedules
☞ Follow-ups to receive articles on time
☞ Bridge the gap between the shipment by the supplier and the receipt of articles by the customer
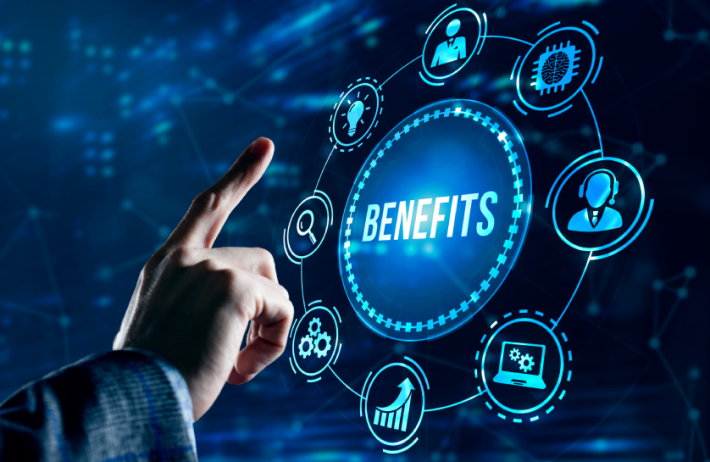
Transition
TIME TAKEN FOR TRANSITION
Step 1
Analysis of requirements – 1 Week
Step 2
Documentation – 2 Weeks
Step 3
Create framework – 2 Weeks
Step 4
Step-by-step implementation – 2 Weeks
Step 5
Transfer – 2 Weeks
For more assistance in understanding the transition process, kindly get in touch with us at contact-wbs@wuerth-industrie.com
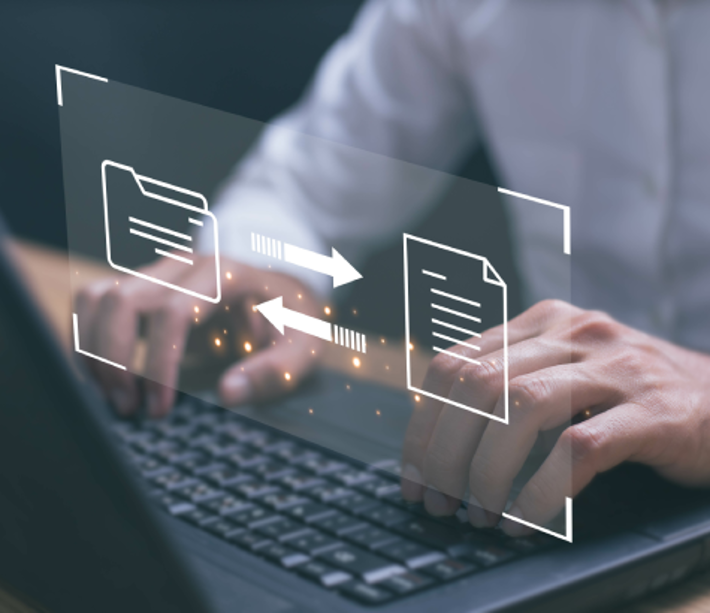
Case study:
Receiving Orders On-Time through the Expediting Process
Introduction:
Effective supply chain management is crucial for businesses to maintain efficient operations and timely deliveries. Our customer, Würth Canada Ltd., recognized the importance of optimizing the Expediting process to ensure prompt response from suppliers and minimize delays. This case study highlights how we successfully transformed the expediting process, resulting in improved communication, enhanced visibility, and streamlined operations.
Problem:
Before implementing the Expediting process, our customer faced significant challenges in receiving timely order confirmations and receiving orders on time. Furthermore, they needed to spend a lot of time in following up with suppliers for pending quotations. Moreover, tracking the Estimated Time of Arrival (ETA) involved extensive manual effort. These issues resulted in limited visibility into supplier responses and posed an increased risk of disruptions to the supply chain.
Solution:
To address these challenges, we implemented a comprehensive solution with the Expediting process. We established a team that would take follow-ups with suppliers regarding the pending quotations. This team enabled standardized communication and reminders through manual emails or calls and ensured that our suppliers received consistent and timely notifications. We integrated the supplier updates with our ERP system. This allowed us to collect and store ETA updates in real-time, offering us immediate visibility into delivery schedules and potential delays.
We also centralized all the Expediting-related data in our ERP system. This included quotations, communication history, and ETA updates. This centralization improved the data accessibility and enhanced an overall data accuracy.
Results:
The implementation of our enhanced Expediting process yielded significant benefits for Würth Canada Ltd. Key results included:
1. Improved Communication: The manual communication ensured consistent and timely follow-ups with suppliers regarding the pending quotations. This improved communication reduced response time and contributed to efficient decision-making.
2. Enhanced Visibility: Real-time tracking of ETA information provided improved visibility into the progress of shipments. This visibility allowed us to proactively address any potential delays and make informed decisions to avoid disruptions.
3. Streamlined Operations and Time Saving: Centralizing Expediting-related data in the ERP system streamlined processes. Furthermore, the data accuracy improved and led to better data integrity and operational efficiency than before. By handling the Expediting process and entering the accurate data, we saved nearly 60.34 hours every month for the customer.
Conclusion:
By optimizing the Expediting process, Würth Canada Ltd. achieved significant improvements in supplier engagement, time-savings, and operational efficiency. The implementation of regular communication, real-time ETA tracking, and data centralization enhanced visibility, reduced delays, and improved overall supply chain management. We remain committed to leveraging technology and process optimization to drive operational excellence, enhance supplier relationships, and achieve greater business success.